Lasertechnologie von EMAG ist aus dem modernen Getriebebau kaum mehr wegzudenken, denn die dazugehörigen ELC-Maschinen (EMAG Laser Cell) ermöglichen einen effektiven Pkw-Leichtbau und sinkende Bauteilkosten. Aktuell ändern die EMAG Laserspezialisten mit Sitz in Heubach bei Schwäbisch Gmünd ihren Namen: Aus „EMAG Automation“ wird „EMAG LaserTec“. Was steckt hinter dieser Entscheidung? – Ein Gespräch mit EMAG LaserTec Geschäftsführer Dr. Andreas Mootz über den wachsenden Erfolg, neue Technologien und interessante Anwendungsbereiche.
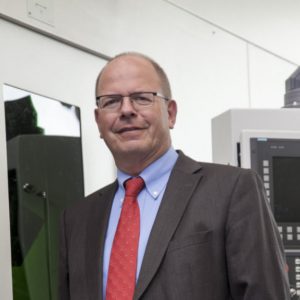
„Unser Verfahren eröffnet große Möglichkeiten für den Leichtbau.“
Herr Dr. Mootz, warum firmiert EMAG Automation ab sofort unter dem Namen „EMAG LaserTec“?
Dazu muss man zunächst einmal wissen, wie rasant sich unsere Kerntechnologie in den letzten Jahren entwickelt hat. Laser-Lösungen machen einen sehr großen Teil unseres Umsatzes am Standort Heubach aus. Außerdem passt der alte Name „EMAG Automation“ schon seit rund zwei Jahren nicht mehr so richtig zu unserem Betätigungsfeld, weil Automationslösungen für die EMAG Gruppe mittlerweile an anderen Standorten entstehen. Von daher ist die aktuelle Umfirmierung nur folgerichtig. Mit dem neuen Namen „EMAG LaserTec“ unterstreichen wir sehr deutlich, welche Bedeutung das Laserschweißen jetzt und in Zukunft für uns hat. Die Technologie wird immer wichtiger.
Woher kommt der große Erfolg der Laserschweiß-Technologie?
Schauen Sie auf das Megathema „Leichtbau“ innerhalb der Automobilindustrie. Praktisch jede zentrale Komponente soll nach Möglichkeit leichter werden. Innerhalb des Getriebebaus ist das aber eine schwierige Anforderung, weil die Gesamtzahl der Bauteile immer weiter ansteigt – zum Beispiel, wenn Hybridantriebe integriert werden oder die Zahl der Gänge im Automatikgetriebe zunimmt. An dieser Stelle punktet unser Laserschweißen, weil es viel schwerere Schraubverbindungen in vielen Bauteilen ersetzt.
Können Sie das mit Zahlen unterstreichen?
Die Schraubverbindung zwischen Ausgleichsgetriebe und Tellerrad ist ein gutes Beispiel. Wenn hier stattdessen eine Schweißverbindung zum Einsatz kommt, ist das Bauteil um rund 1,2 Kilo leichter als vorher. Eine solche Einsparung ist natürlich ein enormer Schritt nach vorne für den Leichtbau. Gleichzeitig sinken übrigens die Kosten für die Bearbeitung der Einzelteile deutlich. Es gibt moderne Doppelkupplungsgetriebe, die 16 verschiedene Laserschweiß-Nähte aufweisen – an den diversen Getrieberädern, der Doppelkupplung und dem Differential.
Wie schätzen Sie Ihre allgemeine Marktposition im Laserschweiß-Bereich ein?
Mittlerweile sind mehr als 160 unserer ELC-Systeme bei praktisch allen führenden Automobilisten im Einsatz – Tendenz stark steigend. Der Grund dafür liegt bei einem echten Alleinstellungsmerkmal: Wir kennen meist den gesamten Produktionsablauf rund um das Laserschweißen und konzipieren die komplette Prozesskette von der Zerspanung über das Schweißen bis hin zu abschließenden Ultraschall-Prüfprozessen. Auf diese Weise ist die Planung von neuen Produktionsstätten und die Erweiterung von bestehenden natürlich massiv vereinfacht. Außerdem kommen bewährte Komponenten des modularen EMAG Maschinenbaus zum Einsatz. Diese Kombination aus ganzheitlichem Verfahrens-Know-how, Bauteil-Wissen und Maschinenbauqualität ist etwas Besonderes. Das wird von unseren Kunden auch so gesehen.
Welche Rolle spielt zukünftig das thermische Fügen als weiteres Spezialgebiet von EMAG LaserTec?
Es bleibt unverändert wichtig. Das verdeutlicht das Beispiel einer „gebauten“ Getriebewelle, die nicht mehr aus einem Stück hergestellt wird. Auf diese Weise lässt sich das Bauteil nicht nur extrem kompakt und leicht fertigen, sondern auch neue Funktionen integrieren. Wir verfügen hier über viel Erfahrungswissen und können unsere Kunden bereits während der Bauteilentwicklung mit unserem Erfahrungswissen und in unserem Applikationslabor unterstützen. Übrigens bleibt auch unser angestammtes Know-how zur Spanntechnik wichtig. Immer schmalere Schweißnähte erfordern einen immer genaueren Rundlauf und eine genaue Positionierung der Bauteile. Unförmige Außenkonturen und grobe Oberflächen machen das Spannen und Greifen zu einer besonderen Herausforderung.
Erweitern Sie Ihr Know-how über die beschriebenen Anwendungen und Technologien hinaus?
Aktuell haben wir zum Beispiel eine ganze Reihe von Anlagen mit integrierten Laser-Reinigungsprozessen geliefert. Dabei werden Prozessrückstände von vorgelagerten Prozessen oder Konservierungsstoffe effektiv vor dem Schweißen oder anderen Verfahren entfernt. Ein entscheidender Vorteil ist dabei, dass sich ein solches Verfahren viel einfacher in eine Produktionslinie einbinden lässt als eine konventionelle Waschanlage, die den eigentlichen Herstellungsprozess ja eher unterbricht. Ähnlich interessant ist darüber hinaus das Laserstrahlhärten, mit dem sich Randschichten mit minimalem Verzug partiell härten lassen. Das Verfahren haben wir bereits ausgiebig in unserem Anwendungslabor in Heubach geprüft und angewandt. Zukünftig kommt es bei Bedarf in unseren Maschinen zum Einsatz.
Welche Marktchancen hat aus Ihrer Sicht die Lasertechnologie?
Wir haben gleich mehrere Erfolgstreiber: Auf der einen Seite steigen die Stückzahlen im Automobilbau weiter an und mit dem sich aktuell abzeichnenden Erfolg von Hybridantrieben wird unsere Technologie noch wichtiger. Schließlich nimmt auf diese Weise zum Beispiel die Zahl von Bauteilen zu, deren Komponenten per Laserschweißen zusammengefügt werden. Auf der anderen Seite gibt es immer mehr Anwendungsbereiche für das Laserschweißen und Fügen. Aktuell bauen wir zum Beispiel die erste ELC-Anlage, die innerhalb der Nutzfahrzeugproduktion zum Einsatz kommt. Auch auf dem Feld der E-Mobilität eröffnen sich neue Möglichkeiten – zum Beispiel bei der Produktion von Rotorwellen, Statoren für Elektromotoren oder Differentialen.