Die Anforderungen an die Wellenbearbeitung haben sich in den letzten Jahren deutlich gewandelt. Steigende Variantenvielfalt bei gleichzeitig sinkenden Losgrößen stellen produzierende Unternehmen vor neue Herausforderungen. Mit der VTC 100 GT präsentiert EMAG eine Maschine, in der die Prozesse Drehen, Schleifen, Bohren und Fräsen mittels angetriebenen Werkzeug miteinander kombiniert werden können. Wie diese Technologieintegration die Fertigung effizienter macht und welche konkreten Vorteile Anwender daraus ziehen können, erläutert Marina Manger, technischer Vertrieb bei der Business Unit Schleifen im Gespräch.
Frau Manger, die VTC 100 GT vereint verschiedene Fertigungsverfahren. Welche konkreten Vorteile bietet diese Kombination dem Anwender und können Sie uns dazu Beispiele nennen?
Die VTC 100 GT ermöglicht die Komplettbearbeitung von Wellen in einer Aufspannung. Das bedeutet, wir können Drehen, Schleifen, Bohren etc. in einem Arbeitsraum durchführen. Aufmaße können unter Umständen reduziert werden, da keine Umspannfehler berücksichtigt werden müssen. Technologische Grenzbereiche werden vermieden.
Ein sehr gutes Beispiel ist die Bearbeitung von Rotorwellen. Diese sind das Herzstück des E-Antriebs und stellen hohe Anforderungen an den Bearbeitungsprozess. In einer Aufspannung werden hier Lager- und Dichtringsitze, der Rotor, Ringnuten und Planschultern bearbeitet.
Für die Hartbearbeitung der Lagersitze wird häufig ein Schleifprozess vorgeschrieben. Dieser wird zur Realisierung eines konstanten Schleifaufmaßes vorgedreht. Die anliegenden Planschultern erfordern keinen Schleifprozess, sondern werden fertig gedreht. Der Dichtringsitz wird ebenfalls vorgedreht und anschließend geschliffen. Hier wird oft eine Rz von 1 bis 3µm drallfrei gefordert. Und auch der Rotor wird erst gedreht und anschließend geschliffen. Die geforderten Zeichnungstoleranzen liegen bei IT6. Die Einhaltung der Toleranzen kann über einen In-Prozess-Messkopf sichergestellt werden.
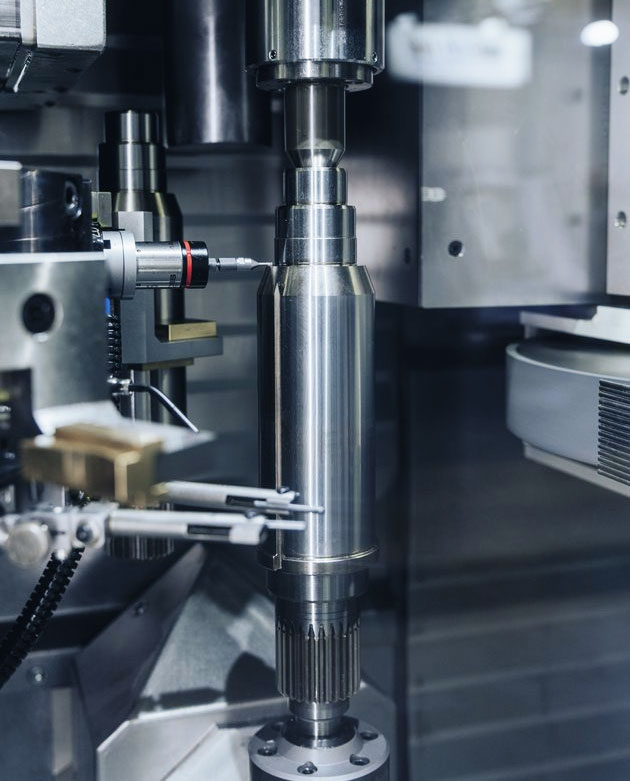
Vertikaler Arbeitsraum der VTC 100 GT mit eingespannter E-Rotorwelle. Die vertikale Anordnung ermöglicht einen optimalen Spänefall. Das Bild zeigt den Messkopf zum Antasten der axialen Position der Rotorwelle und den In-Prozess-Messkopf.
Ein ganz anders Beispiel ist das Folgende: Gelenkgehäuse sollen gedreht und geschliffen werden. Die Bearbeitungsaufgabe ähnelt der für die Rotorwelle. Doch die Jahresstückzahl von 500.000 Werkstücken erfordert ein Umdenken. Bearbeitungsprozesse müssen parallel realisiert werden. Gelöst wurde das mit einer VT 100 als reine Drehmaschine, die über TrackMotion mit einer VTC 100 GT verbunden wurde. Dafür wurde der Revolver der VTC 100 GT mit zwei Greifern ausgestattet. Das ermöglicht einen schnellen Wechsel zwischen Roh- und Fertigteil in der Maschine.
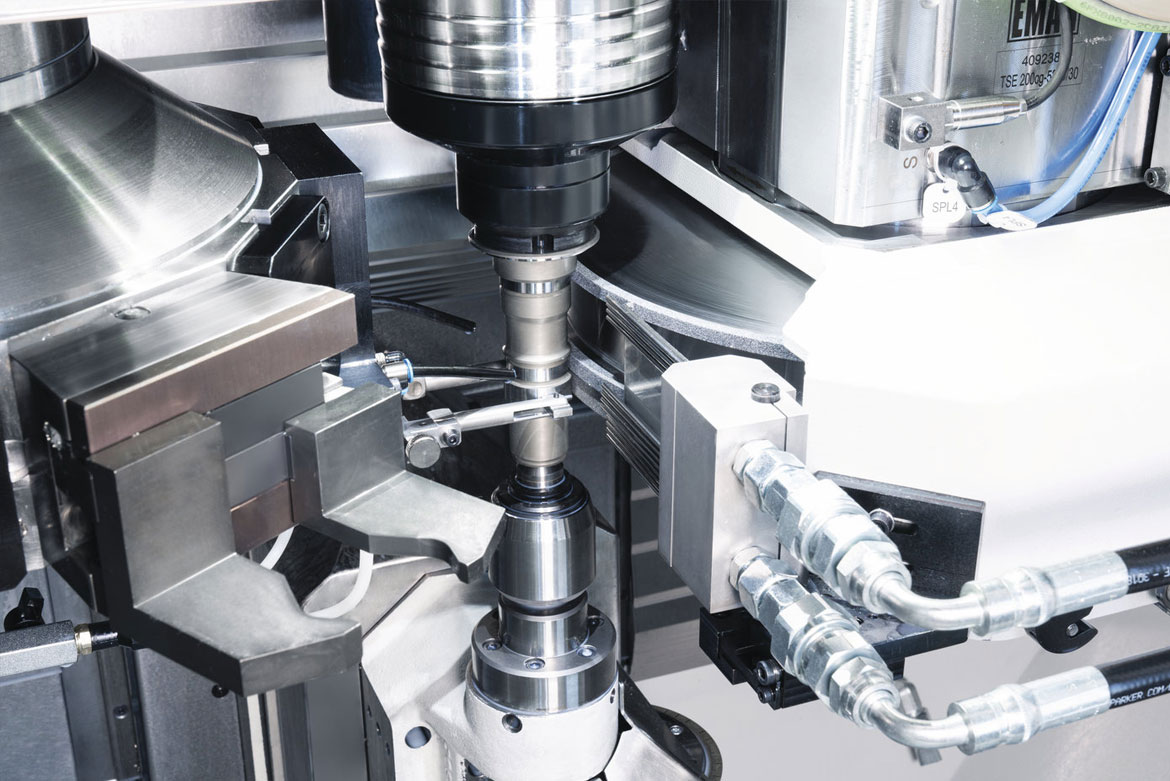
Gelenkgehäuse auf der VTC 100 GT: Die Maschine erreicht bei zwei Schleifoperationen, davon eine drallfrei, eine Taktzeit von 36 Sekunden. Eine Koaxialität der beiden Sitze von ≤ 0,005 mm bei einem Mittenrauhwert von Ra 0,2–0,6 µm.
Die Produktivität spielt bei Fertigungsprozessen eine zentrale Rolle. Wie adressiert die VTC 100 GT diesen Aspekt?
Ein wesentlicher Produktivitätsfaktor ist die automatisierte Be- und Entladung über den Werkzeugrevolver. Zudem verfügt die Maschine über integrierte Roh- und Fertigteilspeicher. Die vertikale Bauweise gewährleistet einen optimalen Spänefall, was die Prozesssicherheit erhöht und Stillstandzeiten minimiert.
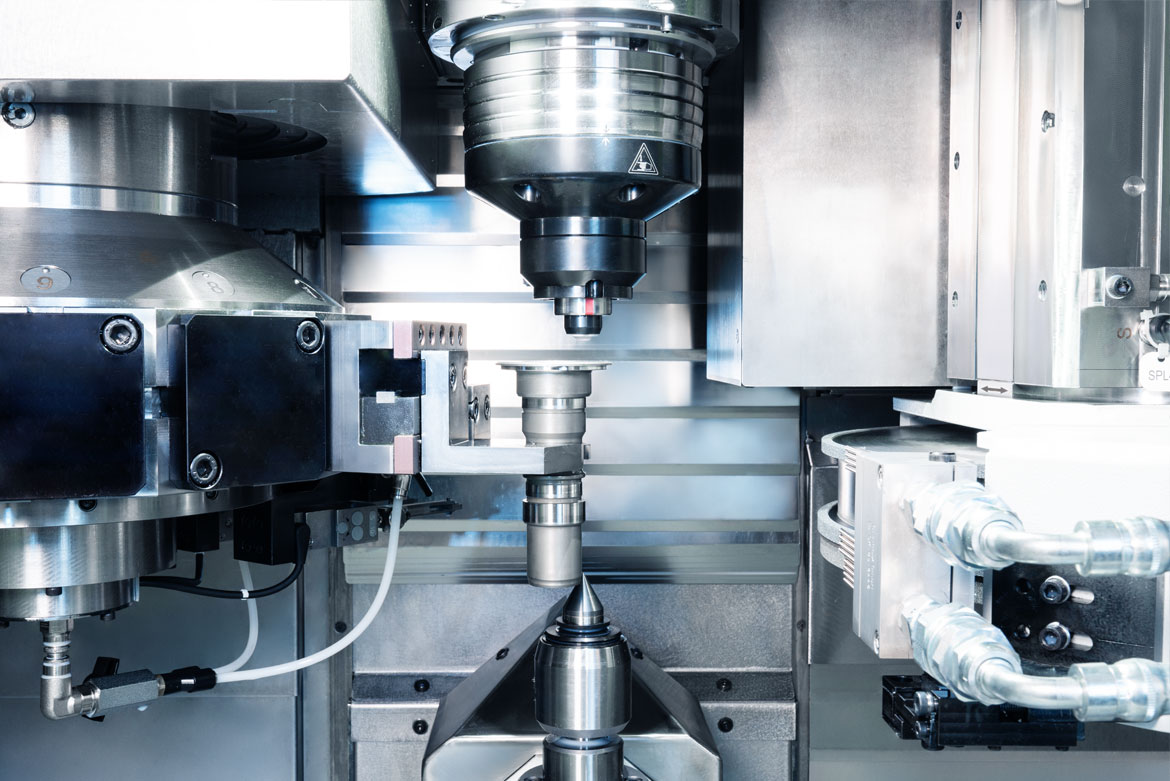
Der Werkzeugrevolver der VTC 100 GT übernimmt neben der Werkzeugaufnahme auch die Be- und Entladefunktion. Das Greifersystem transportiert die Werkstücke zwischen dem integrierten Speicher und der Arbeitsposition, wodurch zusätzliche Handhabungssysteme entfallen.
Wie unterstützt die Maschine Anwender bei häufig wechselnden Bearbeitungsaufgaben?
Die Maschine wurde konsequent auf kurze Rüstzeiten ausgelegt. Durch die sehr gute Zugänglichkeit können Werkzeugwechsel und Rüstprozesse schnell durchgeführt werden. Dies ermöglicht es unseren Kunden, auch bei kleinen Losgrößen wirtschaftlich zu fertigen und flexibel auf neue Bearbeitungsaufgaben zu reagieren.
Viele Produktionshallen haben begrenzte Aufstellflächen. Wie fügt sich die VTC 100 GT hier ein?
Ein großer Vorteil der VTC 100 GT ist der geringe Platzbedarf. Trotz der umfangreichen Funktionalität und des integrierten Werkstückspeichers haben wir bei der VTC 100 GT eine sehr kompakte Bauweise realisiert. Auch die Anbindung eine weiterführende Automation lässt sich problemlos realisieren.
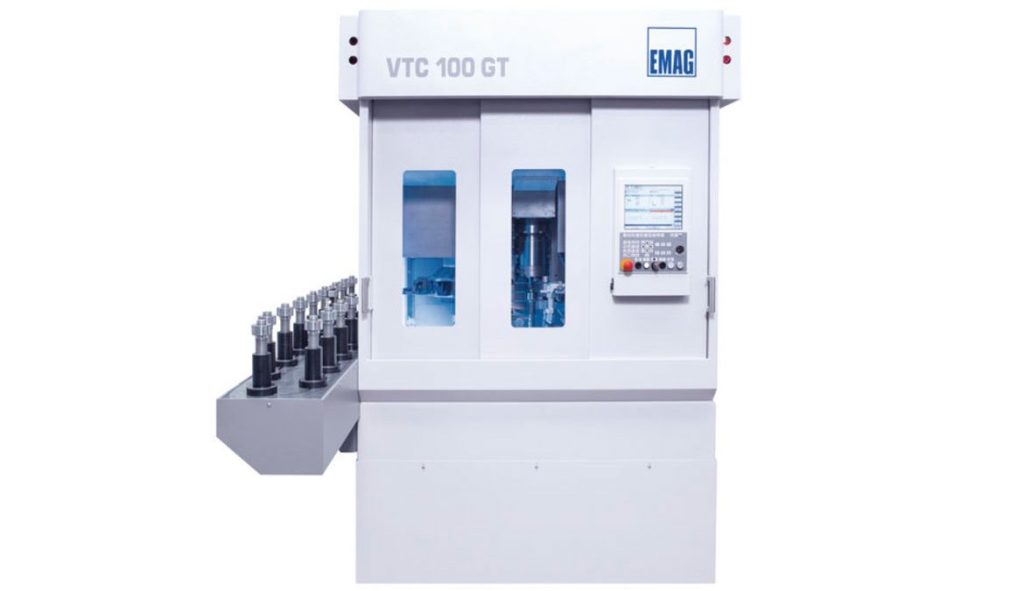
Die VTC 100 GT vereint Schleifen, Hartdrehen und Schälen in einer kompakten Baueinheit. Durch die vertikale Konzeption und die integrierten Speichersysteme wird der Platzbedarf in der Fertigung minimiert, während die Zugänglichkeit für Rüstvorgänge optimal gestaltet ist.