Vertikale Pick-up-Drehmaschinen sind in der modernen Fertigung unverzichtbar. Diese Maschinen produzieren oft im Dreischichtbetrieb und sind bereits stark auf spezifische Produktionsanforderungen optimiert. Doch wie lassen sich bei solch hochentwickelten Fertigungssystemen weitere Leistungssteigerungen erzielen? Mit dieser Frage beschäftigt sich Jürgen Maier, Leiter der Business Unit Drehen bei EMAG. Im folgenden Interview erfahren Sie, wie durch die Direktbeladung mittels Roboter in die Arbeitsspindel einer Vertikaldrehmaschine die Produktivität nochmals gesteigert werden kann.
Für welche Werkstücke eignet sich das Verfahren der Roboter-Direktbeladung besonders?
Das Verfahren der Roboter-Direktbeladung eignet sich besonders für Werkstücke mit kurzen Taktzeiten. Hier haben wir einen entscheidenden Vorteil erreicht: Eine reine Werkstückwechselzeit von nur drei Sekunden. Das ist extrem schnell und effizient. Von der Geometrie her sind stabile Futterteile mit einer zentralen Bohrung ideal. Denken Sie an Zahnräder oder andere Getriebeteile. Solche Werkstücke profitieren besonders von diesem Verfahren. Die Stabilität ist wichtig für die präzise Handhabung durch den Roboter, und die Bohrung ermöglicht eine sichere Aufnahme und Positionierung in der Spindel.
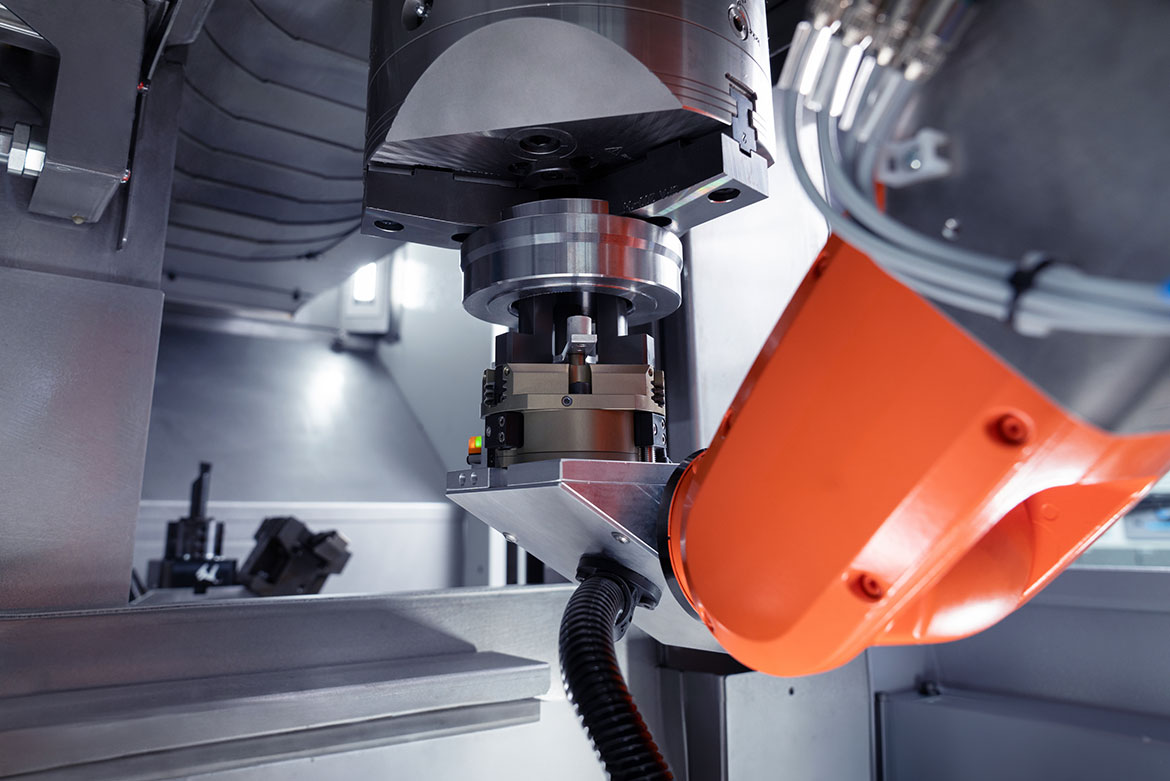
Ein Industrieroboter führt präzise ein Werkstück in die Spindel einer EMAG Vertikaldrehmaschine ein.
Gibt es spezielle Anforderungen an die Geometrie oder Toleranzen der Werkstücke?
Grundsätzlich müssen die Werkstücke natürlich auf die Maschine passen, das ist klar. Ein wesentliches Merkmal ist, dass sie eine Bohrung haben müssen. Das ist entscheidend für die Aufnahme und Positionierung durch den Roboter. Was die Toleranzen angeht, sind wir hier recht flexibel. Auch ausgedrehte Backen sind kein Problem. Das liegt an der hohen Positioniergenauigkeit unseres Roboters. Wir haben ein ausgeklügeltes System entwickelt: Der Roboter arbeitet mit einem Federpaket, gegen das er drückt. Diese Kombination aus präziser Robotersteuerung und mechanischer Feinjustierung ermöglicht es uns, auch bei Werkstücken mit engen Toleranzen zuverlässig zu arbeiten.
Wo liegen die Vorteile gegenüber einer klassischen Pick-up-Beladung?
Die Vorteile der Roboter-Direktbeladung gegenüber der klassischen Pick-up-Beladung sind vielfältig. Erstens, und das ist der Hauptvorteil, sparen wir Taktzeit. Bei der klassischen Methode haben wir einen zusätzlichen Schritt: Das Werkstück wird zunächst auf eine Zwischenstation (Transportband) gelegt und von dort in die Maschine transportiert. Bei unserem Verfahren entfällt dieser Zwischenschritt komplett. Der Roboter legt das Werkstück direkt in die Spindel ein. Das spart nicht nur Zeit, sondern reduziert auch mögliche Fehlerquellen. Zweitens bietet uns diese Methode mehr Flexibilität im Prozessablauf. Wir können zum Beispiel das Spannfutter direkt vor Ort abblasen. Dadurch können wir die Werkstücke noch effizienter handhaben. Ein weiterer wichtiger Vorteil ist die Möglichkeit der sofortigen Nachbearbeitung. Die Teile bleiben im Robotergreifer gespannt, sodass wir sie sofort reinigen, beschriften oder vermessen können. Das optimiert den gesamten Fertigungsprozess und erhöht die Qualität des Endprodukts.
Gibt es Grenzen für dieses Verfahren?
Natürlich gibt es, wie bei jeder Technologie, auch hier Grenzen und Szenarien, in denen klassische Methoden noch Vorteile haben. Unser Verfahren der Roboter-Direktbeladung ist besonders effektiv bei kleineren bis mittleren Vertikaldrehmaschinen, konkret bei unseren Modellen VL 2 und VL 4. Hier macht es absolut Sinn, da wir die volle Effizienz des Systems ausnutzen können. Bei größeren Maschinen, die mit sehr großen und schweren Bauteilen arbeiten, stößt das System an seine Grenzen. In solchen Fällen wird der Prozess oft zu komplex. Man müsste einen überdimensionierten Roboter einsetzen, was weder wirtschaftlich noch praktikabel wäre. Hier bietet die klassische Pick-up-Automatisierung nach wie vor Vorteile. Bei so großen Bauteilen ist die Zeitersparnis in der Be- und Entladung auch weniger kritisch für die Gesamteffizienz.
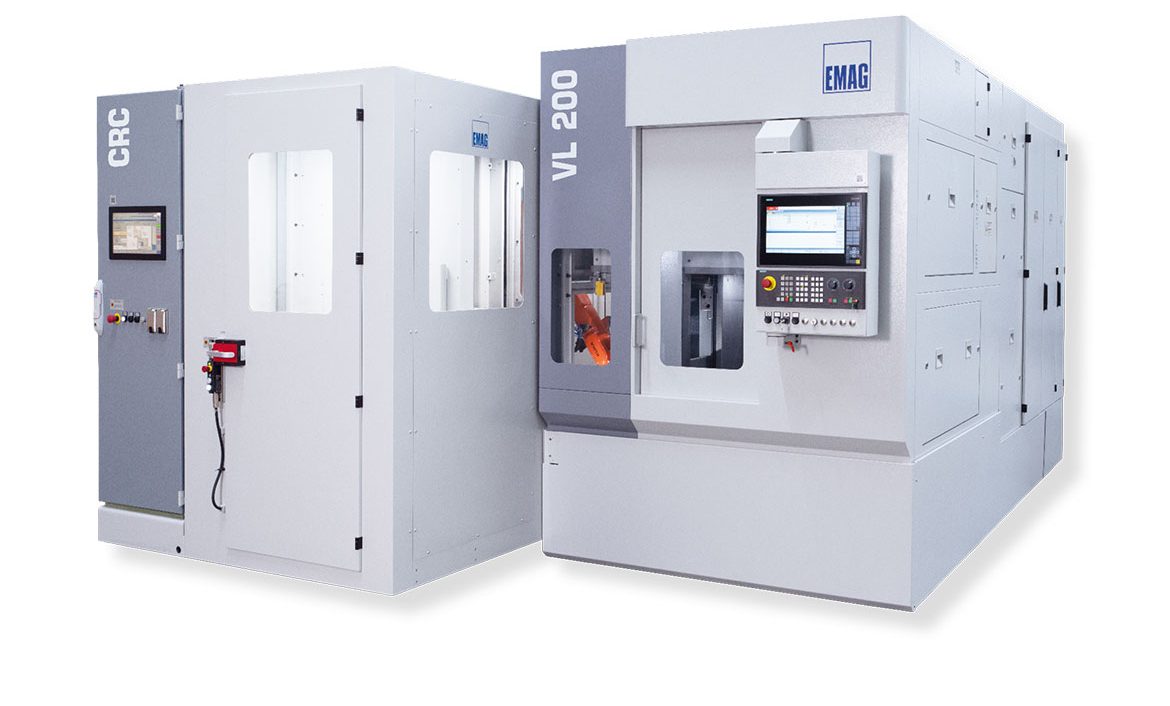
Anstelle eines herkömmlichen Transportbands ist die CRC-Roboterzelle direkt an die VL 200 montiert. Der Roboter lädt das Werkstück unmittelbar in die Spindel und übernimmt die Be- und Entladefunktion mittels eines Doppelgreifers.
Aktuell haben wir die Direktbeladung für Teilegewichte bis 3 kg optimiert. Das deckt einen großen Teil der gängigen Anwendungen ab. Wir haben zwar auch schon erfolgreich mit größeren Teilen gearbeitet, aber das muss immer individuell beurteilt werden. Es muss zur spezifischen Bearbeitungsanforderung und zum Gesamtprozess passen.
Letztendlich geht es darum, für jeden Kunden und jede Anwendung die optimale Lösung zu finden. Manchmal kann das die Roboter-Direktbeladung sein, in anderen Fällen ist vielleicht eine klassische Lösung oder eine Hybridlösung aus Roboter und Pick-up-Automation sinnvoller.
Wie wirkt sich der Robotereinsatz auf die Komplexität des Systems aus?
Interessanterweise macht der Robotereinsatz das Gesamtsystem tatsächlich einfacher, nicht komplexer. Das mag auf den ersten Blick widersprüchlich erscheinen, aber lassen Sie mich das erklären.
Zunächst einmal ist es wichtig zu verstehen, dass moderne Roboter sehr benutzerfreundlich sind. Sobald der Roboter einmal richtig eingerichtet und programmiert ist – wir nennen das „eingeteacht“ – müssen nur noch wenige Positionen eingestellt werden. Das ist ein einmaliger Aufwand, der sich schnell amortisiert. Der große Vorteil liegt in der Flexibilität und Wiederholgenauigkeit des Roboters. Einmal programmiert, führt er die Bewegungen mit höchster Präzision immer wieder aus. Das reduziert die Komplexität im täglichen Betrieb erheblich.
Zudem eliminiert der Roboter die Notwendigkeit für zusätzliche mechanische Komponenten, die bei klassischen Beladesystemen oft erforderlich sind. Jede dieser Komponenten wäre eine potenzielle Fehlerquelle und würde Wartung benötigen. Der Roboter übernimmt all diese Funktionen in einem integrierten System. Die Bedienung der Maschine wird durch den Robotereinsatz nicht komplizierter. Im Gegenteil, viele Prozesse laufen automatisiert ab, was die Bedienung für den Werker an der Maschine vereinfacht.
Zusammengefasst: Obwohl ein Roboter an sich ein komplexes Gerät ist, vereinfacht er in diesem Anwendungsfall das Gesamtsystem; es wird robuster und lässt sich leichter bedienen.
Können Sie uns mehr über die Möglichkeit einer mannlosen Schicht mit diesem System erzählen?
Gerne, das ist einer der Hauptvorteile unseres Systems mit der Roboter-Direktbeladung. Wir können damit eine komplette „Geisterschicht“ fahren, also eine vollständig mannlose Produktion über eine ganze Schicht hinweg. Konkret setzen wir dafür entweder eine CRC-Stapelzelle oder eine SCS-Zelle ein. Diese Zellen sind so konzipiert, dass sie eine große Menge an Rohteilen bevorraten können. Der Roboter greift dann selbstständig auf diese Teile zu und führt den gesamten Be- und Entladeprozess ohne menschliches Eingreifen durch.
Das Resultat ist eine erhebliche Steigerung der Gesamtanlageneffektivität (OEE). Stellen Sie sich vor: Die Maschine kann die ganze Nacht durchlaufen, an Wochenenden oder Feiertagen – immer, auch wenn keine Bediener vor Ort sind. Das erhöht die Produktivität enorm, ohne die Personalkosten zu steigern.
Ein weiterer Vorteil ist die Konstanz der Produktion. Der Roboter arbeitet immer mit der gleichen Geschwindigkeit und Präzision, egal ob es 2 Uhr nachts oder 14 Uhr am Nachmittag ist. Das führt zu einer sehr gleichmäßigen Qualität der produzierten Teile.
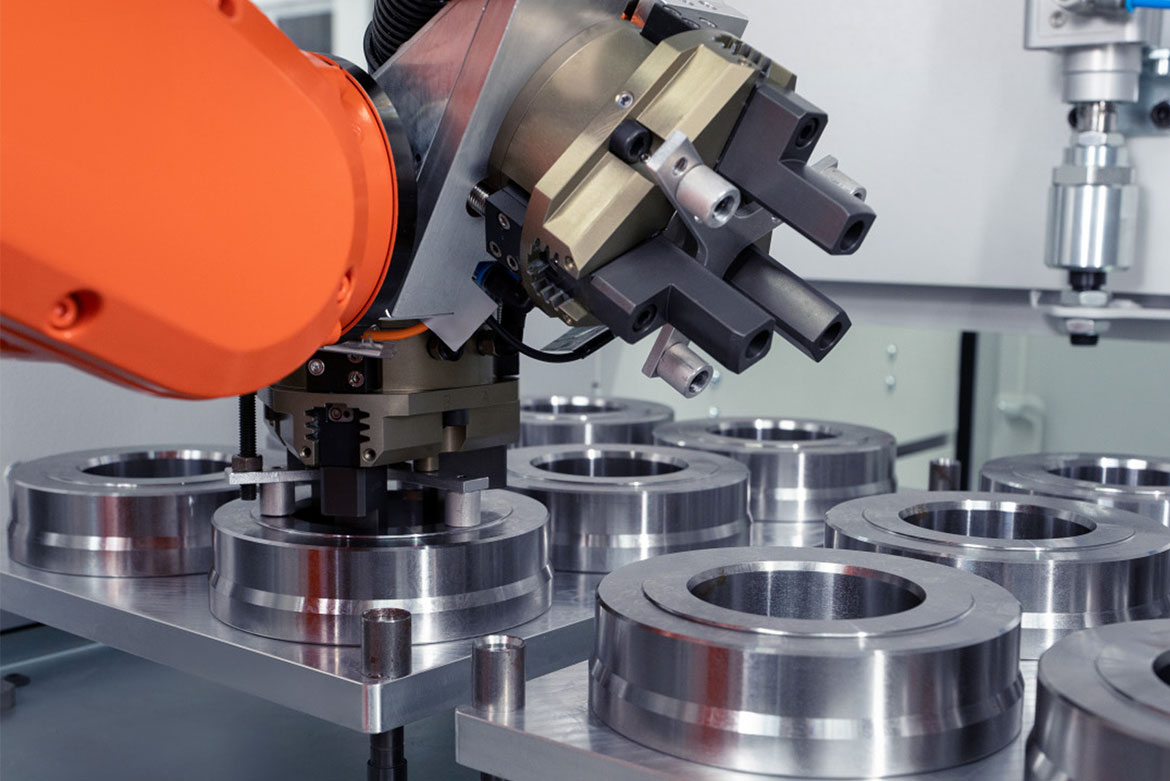
Die CRC-Stapelzelle ermöglicht eine vollautomatische Produktion.
Das klingt beeindruckend. Aber wie stellen Sie sicher, dass die Werkzeuge für eine komplette Schicht ausreichen?
Das ist eine gute Frage, denn die Werkzeugstandzeit ist tatsächlich oft der limitierende Faktor bei langen, mannlosen Produktionsläufen. Hier kommt unser 12-fach-Werkzeugrevolver ins Spiel, der eine Schlüsselrolle in diesem System einnimmt.
Der 12-fach-Revolver bietet uns die Möglichkeit, mit Schwesterwerkzeugen zu arbeiten. Das bedeutet, wir können mehrere identische oder sehr ähnliche Werkzeuge in den Revolver einsetzen. Wenn ein Werkzeug seine Standzeit erreicht hat, schaltet das System automatisch auf das nächste Schwesterwerkzeug um.
Lassen Sie mich das an einem Beispiel verdeutlichen: Angenommen, wir haben einen Bearbeitungsprozess, der vier verschiedene Werkzeuge benötigt. In einem herkömmlichen System würden diese vier Werkzeuge die maximale Laufzeit bestimmen. Mit unserem 12-fach-Revolver können wir jedoch jedes dieser Werkzeuge dreifach bestücken. Das verdreifacht effektiv unsere mögliche Laufzeit ohne Werkzeugwechsel.
Zusätzlich nutzen wir fortschrittliche Verschleißüberwachungssysteme. Diese überwachen kontinuierlich den Zustand der Werkzeuge und können präzise vorhersagen, wann ein Werkzeugwechsel nötig wird. So stellen wir sicher, dass wir die Schwesterwerkzeuge optimal nutzen und die Produktion nicht wegen eines unerwarteten Werkzeugausfalls unterbrochen wird.
Diese Kombination aus hoher Werkzeugkapazität und intelligentem Werkzeugmanagement ermöglicht es uns, eine komplette Schicht – ob 8, 10 oder sogar 12 Stunden – mannlos zu produzieren. Dies ist ein entscheidender Faktor für die Realisierung wirklich effizienter mannloser Schichten.
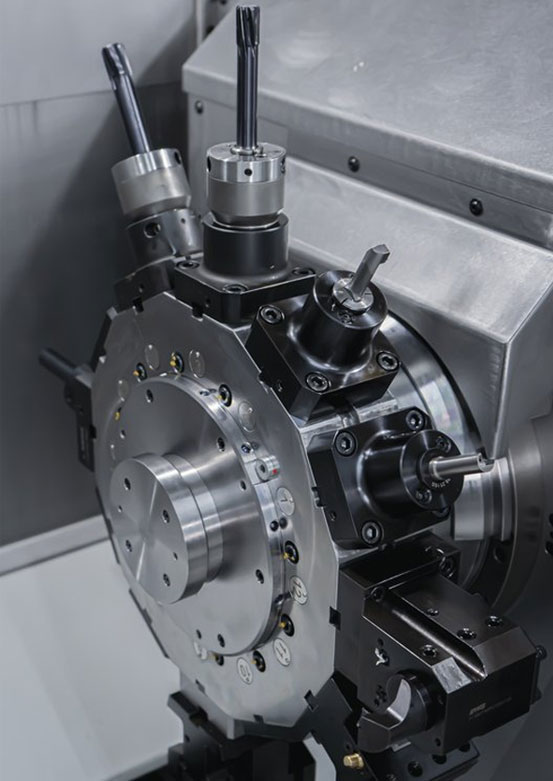
Nahaufnahme des 12-fach-Werkzeugrevolvers, der verschiedene Werkzeuge für die mannlose Produktion bereithält.
Das klingt nach einem sehr durchdachten System. Welche Vorteile ergeben sich daraus für die Kunden?
Die Vorteile für unsere Kunden sind vielfältig:
- Erhöhte Produktivität: Durch die Möglichkeit, 24/7 zu produzieren, können unsere Kunden ihre Auslastung und damit ihre Gesamtproduktion erheblich steigern.
- Kosteneffizienz: Mannlose Schichten reduzieren die Personalkosten pro produziertem Teil signifikant.
- Flexibilität: Das System kann problemlos Nachtschichten, Wochenenden oder Feiertage abdecken, ohne dass zusätzliches Personal eingeplant werden muss.
- Konstante Qualität: Unsere Maschinen und der Roboter arbeiten immer mit der gleichen Präzision, was zu einer sehr gleichmäßigen Teilequalität führt.
- Optimierte Ressourcennutzung: Durch die intelligente Nutzung des 12-fach-Revolvers und der Schwesterwerkzeuge wird die Standzeit der Werkzeuge optimal ausgenutzt.
- Reduzierter Planungsaufwand: Einmal eingerichtet, kann das System lange Produktionsläufe ohne ständige Überwachung durchführen.
- Wettbewerbsvorteil: Die Fähigkeit, flexibel und kostengünstig zu produzieren, kann in vielen Branchen einen entscheidenden Wettbewerbsvorteil darstellen.
Zusammengefasst ermöglicht unser System unseren Kunden, ihre Produktion zu optimieren, Kosten zu senken und gleichzeitig ihre Flexibilität und Reaktionsfähigkeit auf Marktanforderungen zu erhöhen.