Die CLC 200 ist eine leistungsstarke Wälzfräsmaschine, die speziell für die Bearbeitung von Zahnrädern, verzahnte Wellen und Schneckenräder bis Modul 5 entwickelt wurde. In diesem Interview gibt Alexander Morhard, Technical Sales Support Manager bei EMAG SU, einen Überblick über die wichtigsten Merkmale, Vorteile und Einsatzgebiete.
Herr Morhard, können Sie uns zunächst die Hauptmerkmale dieser Maschine erläutern?
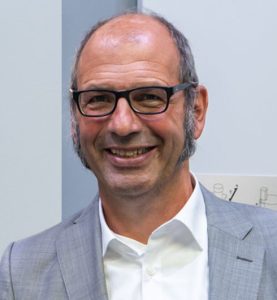
Alexander Morhard_EMAG SU
Die CLC 200 ist eine robuste Vertikal-Wälzfräsmaschine. Ihr stabiler und schwerer Aufbau mit einem Maschinengewicht von über 12 Tonnen dämpft Schwingungen sehr effektiv. Herzstück der Maschine sind die Direktantriebe sowohl im Tisch als auch im Fräskopf. Diese eliminieren jegliches Getriebespiel zwischen Tisch und Fräskopf und erzeugen so qualitativ hochwertige Verzahnungen. Der Fräskopf ist aus Stahlguss gefertigt und besitzt eine V-förmige, geschliffene und handgeschabte Tangentialachse mit hoher Steifigkeit und sehr guter Dämpfung. Aufgrund der besonderen Konstruktion des Fräskopfes, ermöglicht durch dessen Beschaffenheit aus einem hochfesten Werkstoff, lassen sich große Schwenkwinkel realisieren.
Der Fräsdorn ist mit zwei Präzisionskegeln gelagert, die exakt zueinander laufen und einen sehr guten Rundlauf des Fräsers gewährleisten, was für die Verzahnungsqualität entscheidend ist und zudem ein schnelles Umrüsten des Fräsers ermöglicht. Ein automatisch verfahrbares Gegenlager im Fräskopf sorgt für eine steife Aufspannung der Werkzeuge und erleichtert ebenfalls das Einrichten. Dank dieser Konstruktion können wir nicht nur Bohrungsfräser, sondern auch Schaftfräser mit höchster Präzision einsetzen, was die Flexibilität der Maschine enorm erhöht. Neben dem Standard-Fräskopf kann auch optional ein Hochgeschwindigkeits-Fräskopf installiert werden. Auch der direkt angetriebene Werkzeugtisch kann optional mit höheren Drehzahlen ausgerüstet werden.
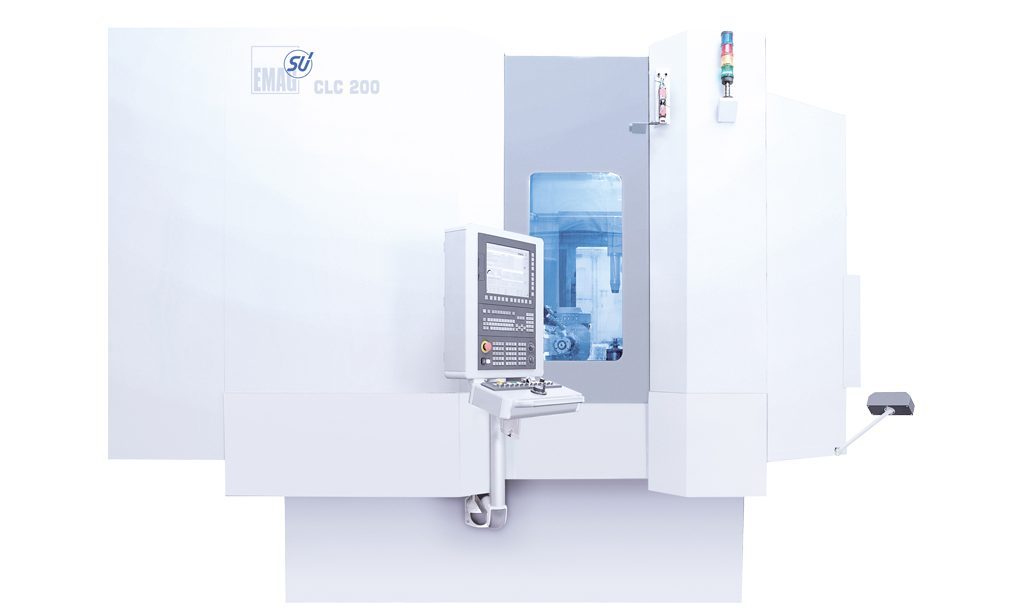
Vertikal-Wälzfräsmaschine CLC 200 von EMAG in kompakter Bauweise und mit robuster Konstruktion.
Das klingt nach einer sehr durchdachten Konstruktion. Welche weiteren Besonderheiten gibt es?
Neben dem hochpräzisen Fräskopf verfügt die CLC 200 über einen automatisch verfahrbaren Reitstock. Dieser kann Werkstücke bis zu einer Länge von 600 mm optimal abstützen und über die NC im Anpressdruck justiert werden. So kann bei schlanken Wellen gewährleitet werden, dass diese sich während der Bearbeitung lediglich minimal durchbiegen.
Ein weiteres Highlight ist der Ringlader mit zwei NC-Achsen. Hier lässt sich über die NC-Steuerung der Hub und die Drehung des Ringladers eingestellen. Durch das automatische Anfahren der Greifposition am Werkstück können die Werkstücke mit einer minimalen Anzahl von Greifarmen automatisch beladen werden. Dies verkürzt den Rüstvorgang drastisch und spart natürlich Kosten, da keine teuren Greiferarme beschafft und gelagert werden müssen.
Die Maschine ist auch hinsichtlich der Kühlmittel sehr flexibel. Sie kann mit Wasser, Emulsion oder auch trocken betrieben werden.
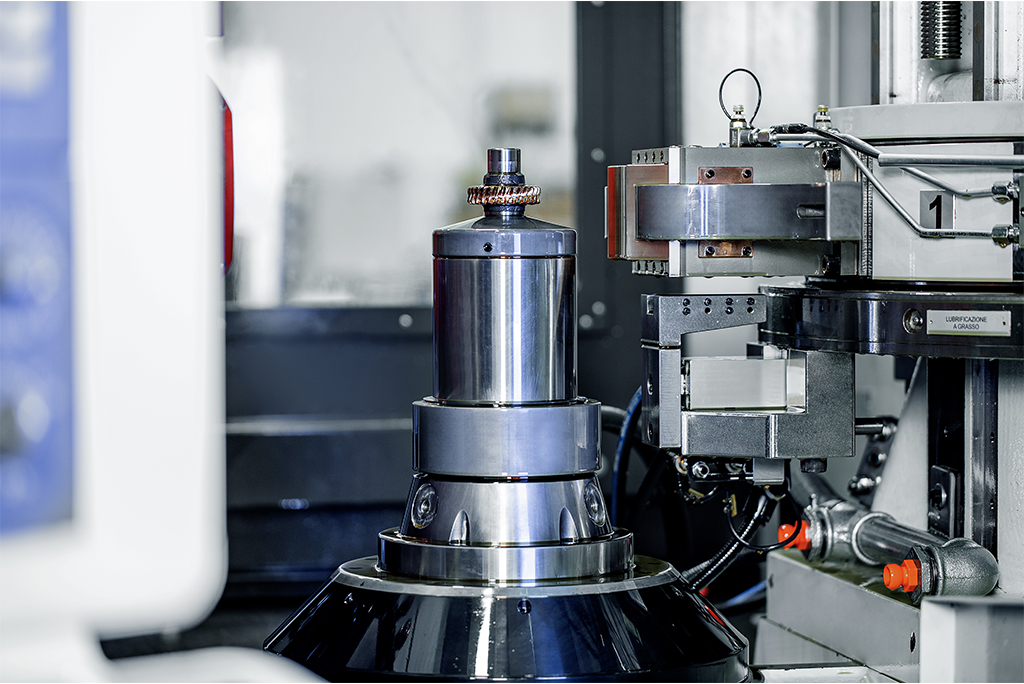
NC-Ringlader mit schwenkbaren Armen für den Einsatz von Wälzfräsern mit kleinem Durchmesser an der CLC 200 Wälzfräsmaschine. Diese spezielle Konfiguration ermöglicht es, Wälzfräser mit kleinem Durchmesser einzusetzen, um auch komplexe und filigrane Werkstücke präzise zu bearbeiten.
Für welche Branchen und Anwendungen ist die Wälzfräsmaschine besonders geeignet?
Die CLC 200 ist ein wahres Multitalent. Sie eignet sich hervorragend für Lohnverzahner, die eine hohe Flexibilität benötigen. Im Getriebebau glänzt sie durch Präzision und Zuverlässigkeit. Die Automobilindustrie schätzt besonders ihre Fähigkeit, komplexe Verzahnungen in einem Arbeitsgang zu fertigen. Konkret können Zahnräder, Zahnwellen und Schneckenräder bis Modul 5 bearbeitet werden. Der maximale Werkstückdurchmesser beträgt 220 mm im Durchmesser und 600 mm in der Länge. Es können gerad- und schrägverzahnte Zahnräder hergestellt werden. Die Maschine ist so ausgelegt, dass sie sowohl für die Großserienfertigung als auch für die Einzelteilfertigung wirtschaftlich eingesetzt werden kann.
Wie flexibel ist die CLC 200 in Bezug auf verschiedene Bearbeitungstechnologien?
Die Flexibilität der CLC 200 ist wirklich beeindruckend. Wir können Verzahnungen vorfräsen zum Schleifen, Fertigfräsen, Fräsen mit Scheibenfräser und Schälwälzfräsen. Das Schälwälzfräsen, eine Technologie der Hartfeinbearbeitung, benötig hier optional einen Einmittsensor, der automatisch eingeschwenkt werden kann. Beim Einzelteilfräsen nutzen wir die hohe Dynamik der Maschine, wodurch sich auch komplexe Verzahnungsgeometrien sehr wirtschaftlich fertigen lassen. Der Wechsel zwischen diesen Technologien ist denkbar einfach und erfordert nur sehr kurze Rüstzeiten.
Wie erfolgt die Steuerung dieser verschiedenen Prozesse?
Wir bieten zwei Optionen an: Die Fanuc-Steuerung oder optional die Siemens-Steuerung mit einem speziell für die schnelle Programmierung von Wälzfräsprozessen entwickelten HMI. Beide Systeme ermöglichen eine intuitive Dialogprogrammierung. Die EMAG Dialogprogrammierung bietet Eingabemasken für alle gängigen Verzahnungsarten. Der Bediener muss lediglich die Werkstück- und Werkzeugdaten eingeben und die Steuerung berechnet automatisch alle notwendigen Bewegungen. Hierdurch lassen sich Anlernzeiten für neue Mitarbeiter reduzieren und Falscheingaben minimieren.
Lassen Sie uns über den Ringlader der CLC 200 sprechen. Welche Vorteile bietet er?
Der NC-gesteuerte Ringlader ist ein echtes Automatisierungs-Allroundtalent. Mit seinen zwei NC-Achsen, der Drehachse und der Hubachse, lassen sich nahezu alle Beladeaufgaben meistern. Die Drehachse ermöglicht eine Drehung um 180 Grad, während die Hubachse einen großen Verfahrweg hat. Damit können wir Werkstücke unterschiedlichster Größe ohne Umrüsten handhaben. Ein entscheidender Vorteil ist die Reduzierung der Rüstteile. Statt für jede Werkstückgröße spezielle Greifer vorzuhalten, fahren wir einfach die passende Position an. Das spart nicht nur Kosten, sondern auch wertvolle Rüstzeit. Die Zuverlässigkeit des Systems überzeugt. Einige unserer Kunden setzen den Ringlader seit Jahren ohne nennenswerte Ausfälle im Dreischichtbetrieb ein.
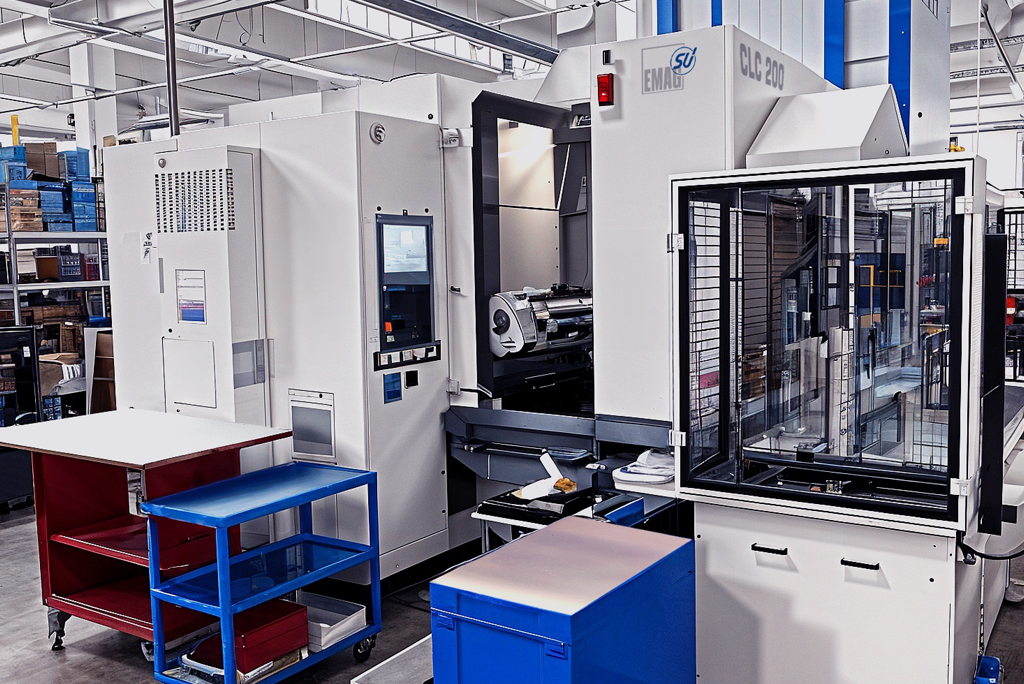
Der NC-gesteuerte Ringlader der CLC 200 beim Be- und Entladen eines Werkstücks, was die Effizienz der Automation verdeutlicht.
Wie einfach ist die Bedienung des Ringladers?
Die Bedienung ist sehr einfach und intuitiv. Der Bediener gibt lediglich die Greiferhöhe und den Werkstückdurchmesser in die Steuerung ein. Der Rest vollzieht sich automatisch. Am Zuführband müssen lediglich die Werkstückträger gewechselt werden, was dank Schnellverschlüssen in wenigen Sekunden erledigt ist. Eine Besonderheit ist die integrierte Werkstückerkennung. Hierbei wird automatisch geprüft, ob das richtige Werkstück vorhanden ist und stoppt bei Abweichungen den Prozess. Das vermeidet Ausschuss und erhöht die Prozesssicherheit enorm.
Gibt es alternative Automatisierungslösungen für die CLC 200?
Ja, neben dem Ringlader bieten wir auch eine Roboterbeladung an. Dabei steht ein 6-Achs-Roboter hinter der Maschine und belädt direkt auf die Spindel. Die CLC 200 ist dafür mit einer automatischen Schiebetür ausgestattet. Der Roboter benötigt für einen kompletten Beladezyklus zwar etwas länger als der Ringlader, ist dafür aber flexibler. So kann er beispielsweise Werkstücke in eine Entgrat- oder Reinigungsstation entgraten bzw. säubern oder in einer Messstation prüfen. Das ist der Vorteil des Roboters, er kann neben dem Be- und Entladen auch andere Aufgaben übernehmen. Für Kunden mit komplexen Werkstücken, langen Laufzeiten oder häufig wechselnden Teilefamilien kann die Roboterlösung daher die bessere Wahl sein, das hängt immer vom Einzelfall ab. Auch die Bedientür kann optional automatisch geöffnet werden.
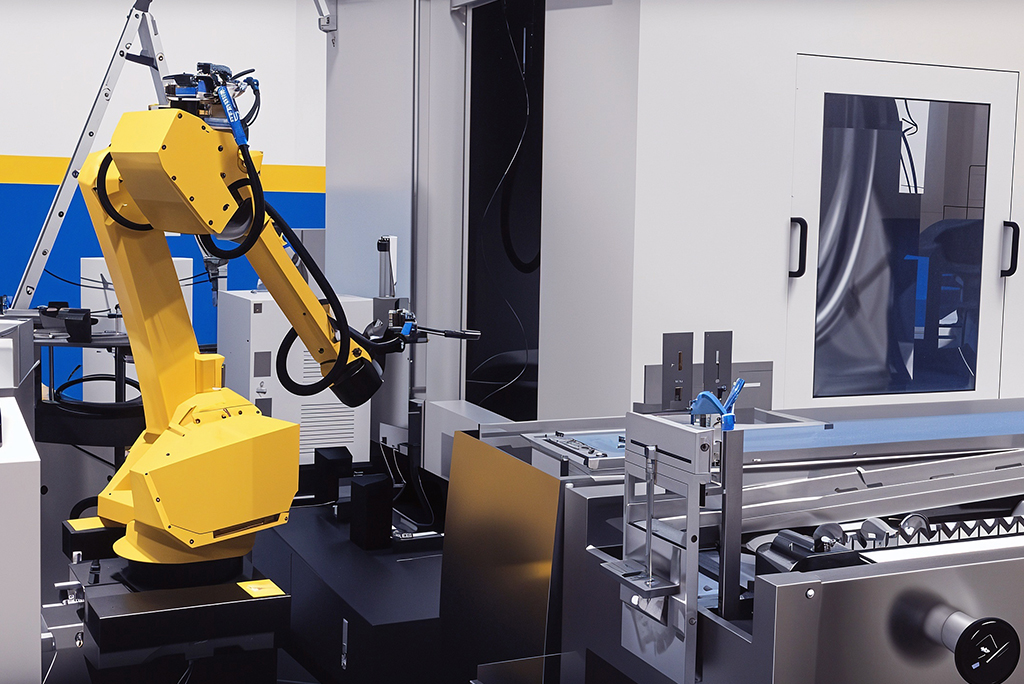
An der Rückseite der CLC 200 Wälzfräsmaschine ist ein Roboter positioniert, der ein Werkstück durch eine geöffnete Beladetür in die Maschine lädt. Diese Konfiguration ermöglicht eine effiziente und schnelle Produktion, da der Roboter parallel zur Bearbeitung weitere Werkstücke vorbereiten kann.
Wie wird die Werkstückkontrolle und Lageorientierung bei der CLC 200 realisiert?
Die CLC 200 bietet ein umfassendes Paket zur Werkstückkontrolle und Lageorientierung. Im Tisch befindet sich ein hydraulischer Zylinder zur automatischen Betätigung der Werkstückaufspannung. Der Spannweg wird digital überwacht, um Fehler bei der Aufspannung sofort zu erkennen. Für das lageorientierte Fräsen zu einer Nut, Bohrung oder Verzahnung setzen wir einen hochpräzisen induktiven Sensor ein. Dieser ermittelt die exakte Lage des Werkstücks und positioniert die zu fräsende Verzahnung hierzu. Zusätzlich verfügt die Maschine optional über ein integriertes Messsystem. Dieses kann sowohl für lageorientierte Werkstücke als auch für die Kontrolle der produzierten Verzahnung eingesetzt werden. Nach der Bearbeitung führt es eine 100%-Kontrolle durch, um sicherzustellen, dass alle Qualitätsparameter eingehalten wurden. Ein besonderes Feature ist die adaptive Prozessregelung. Basierend auf den Messergebnissen kann die Steuerung automatisch Anpassungen an den Bearbeitungsparametern vornehmen, um Schwankungen in der Materialqualität oder Werkzeugverschleiß zu kompensieren.
Sie erwähnten die Direktantriebe im Werkstücktisch und im Fräskopf. Welche Vorteile bieten diese?
Die Direktantriebe sind das Herzstück der CLC 200 und ein entscheidender Vorteil. Im Fräskopf eliminieren sie jegliches Getriebespiel, was zu einer sehr hohen Präzision führt.
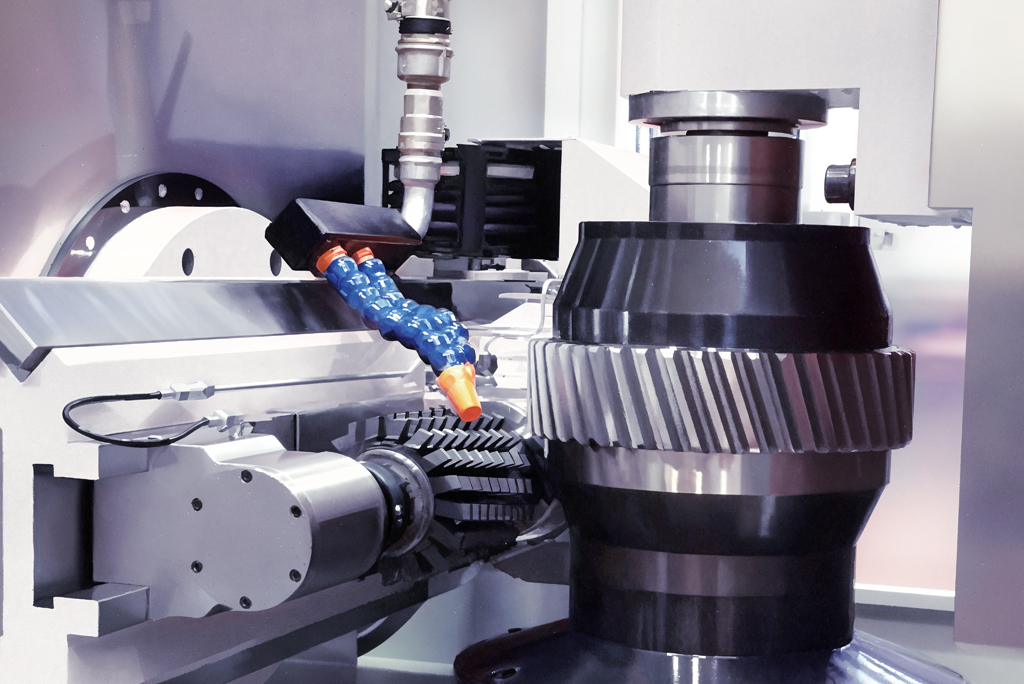
Fräskopf mit Direktantrieb, der für höchste Präzision bei der Zahnradfertigung sorgt.
Der Direktantrieb im Werkstücktisch ist in unterschiedlichen Drehzahlen verfügbar und ermöglicht hohe Drehzahlen bei gleichzeitig höchster Positioniergenauigkeit. Dies ist besonders wichtig beim Wälzfräsen, bei dem es auf einen perfekten Gleichlauf zwischen Werkstück und Fräser ankommt. Ein weiterer Vorteil ist die hohe Lebensdauer. Direktantriebe sind praktisch verschleißfrei, was die Wartungskosten drastisch reduziert und die Verfügbarkeit der Maschine erhöht. Wir haben Kunden, die ihre CLC 200 seit mehreren Jahren im Dreischichtbetrieb einsetzen, ohne dass die Präzision nachgelassen hätte. Ein oft übersehener Vorteil ist die Energieeffizienz. Direktantriebe haben einen Wirkungsgrad von über 90 %, während konventionelle Antriebe oft nur 60 bis 70 % erreichen. Das macht sich in der Stromrechnung deutlich bemerkbar.