Los tornos verticales con sistema pick-up son indispensables en la fabricación moderna. Estas máquinas suelen producir en tres turnos y están altamente optimizadas para cumplir con requisitos de producción específicos. Pero, ¿cómo es posible aumentar aún más el rendimiento en sistemas de fabricación tan avanzados? Jürgen Maier, director de la unidad de negocio de torneado en EMAG, aborda esta cuestión. En la siguiente entrevista, conocerá cómo la carga directa mediante un robot hacia el husillo de trabajo de un torno vertical puede incrementar aún más la productividad.
¿Para qué piezas de trabajo es especialmente adecuado el proceso de carga directa por robot?
El proceso de carga directa por robot es especialmente adecuado para piezas de trabajo con tiempos de ciclo cortos. Aquí hemos logrado una ventaja decisiva: un tiempo de cambio de pieza de sólo tres segundos. Esto es extremadamente rápido y eficiente. En cuanto a la geometría, las piezas de tipo Chuck (sujeción por plato) estables con agujero central son ideales. Piense en engranes u otras piezas de transmisión. Estas piezas de trabajo se benefician especialmente de este proceso. La estabilidad es importante para que el robot pueda manipularlas con precisión, y el taladro permite una recogida y posicionamiento seguros en el husillo.
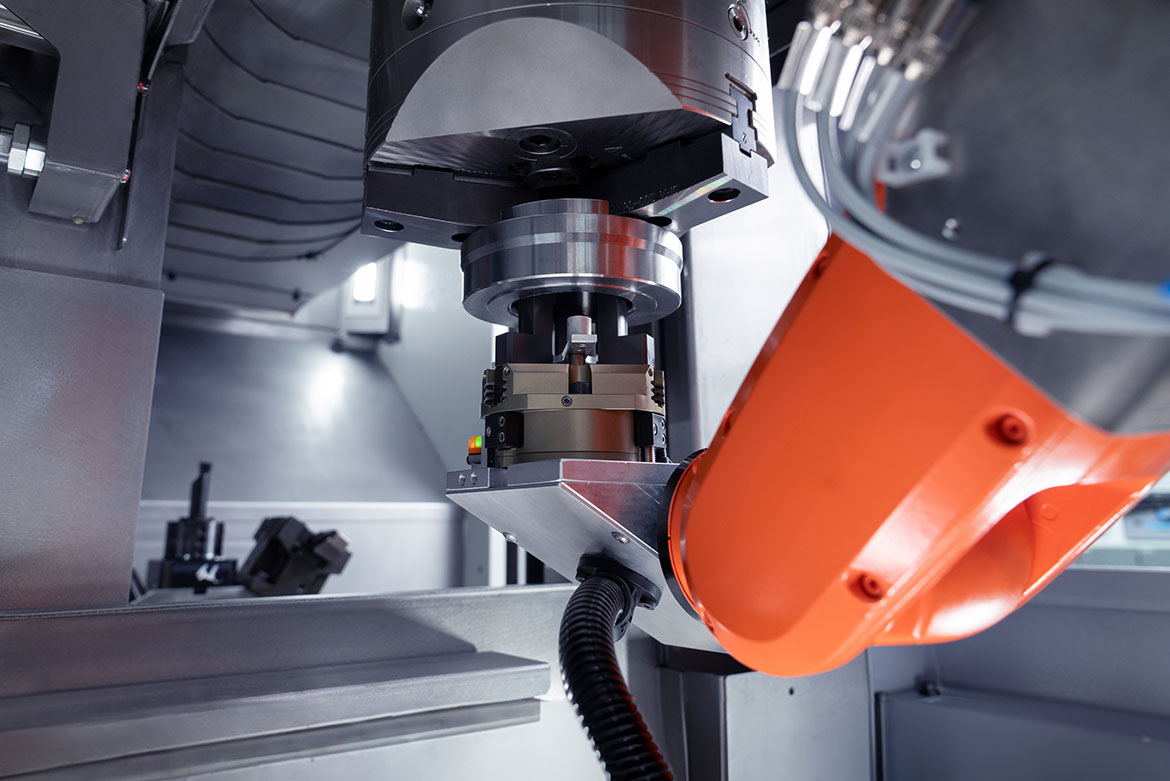
Un robot industrial introduce con precisión una pieza de trabajo en el husillo de un torno vertical EMAG.
¿Existen requisitos especiales en cuanto a la geometría o las tolerancias de las piezas de trabajo?
En general, las piezas de trabajo tienen que caber en la máquina, eso es un hecho. Una característica clave es que deben tener un agujero. Esto es fundamental para que el robot pueda sujetarlas y colocarlas correctamente. En cuanto a las tolerancias, somos bastante flexibles. Incluso las mordazas torneadas no representan un problema. Esto se debe a la alta precisión de posicionamiento de nuestro robot. Hemos desarrollado un sistema sofisticado: El robot trabaja con un conjunto de muelles, sobre el cual ejerce presión. Esta combinación entre un control robótico preciso y un ajuste mecánico fino nos permite trabajar de forma confiable, incluso con piezas que tienen tolerancias muy estrictas.
¿Cuáles son las ventajas con respecto a la clásica carga con pick-up?
Las ventajas de la carga directa con robot en comparación con el método clásico de pick-up son varias. La principal, y más importante, es el ahorro en el tiempo de ciclo. En el método tradicional, hay un paso adicional: la pieza primero se coloca en una estación intermedia (como una banda transportadora), y de ahí pasa a la máquina. Con nuestro sistema, ese paso se elimina por completo. El robot coloca la pieza directamente en el husillo. Esto no solo ahorra tiempo, sino que también reduce posibles fuentes de error. Otra ventaja importante es la mayor flexibilidad en el flujo del proceso. Por ejemplo, podemos soplar el Chuck directamente en el punto de carga, lo que nos permite manipular las piezas de manera aún más eficiente. Además, un beneficio clave es la posibilidad de realizar trabajos inmediatos. Las piezas permanecen sujetas en la pinza del robot, lo que nos permite limpiarlas, marcarlas o medirlas de inmediato. Esto optimiza todo el proceso de fabricación y mejora la calidad del producto final.
¿Existen límites para este procedimiento?
Por supuesto, como con cualquier tecnología, existen límites y situaciones en los que los métodos convencionales siguen teniendo sus ventajas. Nuestro sistema de carga directa por robot es especialmente eficaz en tornos verticales pequeño y mediano, concretamente para nuestros modelos VL 2 y VL 4, donde tiene todo el sentido, ya que aprovechamos al máximo la eficiencia del sistema. Sin embargo, en máquinas más grandes que trabajan con piezas muy grandes y pesadas, el sistema muestra sus límites. En estos casos, el proceso suele resultar demasiado complejo. Habría que utilizar un robot de gran tamaño, lo cual no sería ni rentable ni práctico. Aquí es donde la automatización clásica tipo pick-up sigue siendo la mejor opción. Además, Con piezas tan grandes, el tiempo que se ahorra en la carga y descarga no tiene un impacto tan significativo en la eficiencia total del proceso.
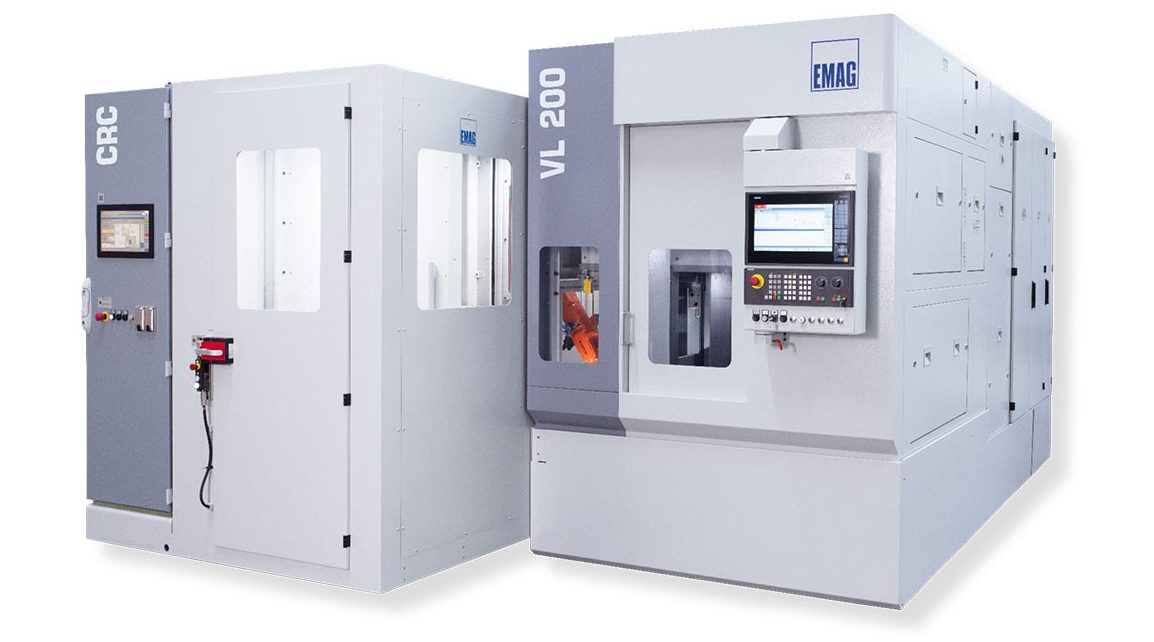
En lugar de una banda transportadora convencional, la celda robótica CRC está instalada directamente en la VL 200. El robot carga la pieza de trabajo directamente en el husillo y se encarga de las funciones de carga/descarga mediante una pinza doble.
Actualmente hemos optimizado la carga directa para piezas de hasta 3 kg de peso. Eso cubre una gran parte de las aplicaciones más comunes. Si bien ya hemos trabajado con éxito con piezas más grandes, cada caso debe evaluarse de manera individual. Tiene que ajustarse a los requerimientos específicos del mecanizado y al proceso completo.
Al final, se trata de encontrar la solución óptima para cada cliente y cada aplicación. A veces, esa solución será la carga directa con robot, pero en otros casos puede ser más adecuado un sistema clásico o incluso una solución híbrida que combine robot y automatización tipo pick-up.
¿Cómo afecta el uso de robots a la complejidad del sistema?
Curiosamente, el uso de robots en realidad hace que el sistema global sea más simple, no más complejo. Esto puede parecer contradictorio a primera vista, pero permítame explicarlo.
En primer lugar, es importante entender que los robots modernos son muy fáciles de usar. Una vez que el robot ha sido instalado y programado correctamente, lo que llamamos “aprendizaje” solo es necesario ajustar unas cuantas posiciones. Se trata de un esfuerzo único que se recupera rápidamente. Se trata de un esfuerzo único que se amortiza rápidamente. La gran ventaja está en la flexibilidad y la repetición del robot. Una vez programado, ejecuta los movimientos una y otra vez con la máxima precisión. Esto reduce considerablemente la complejidad del funcionamiento diario.
Además, el robot elimina la necesidad de componentes mecánicos adicionales que suelen ser necesarios en los sistemas de carga tradicionales. Cada uno de esos componentes representa una posible fuente de fallas y requiere mantenimiento. En cambio, el robot asume todas esas funciones en un sistema integrado. El uso del robot no hace más complicada la operación de la máquina; al contrario, muchos procesos se automatizan, lo que facilita el trabajo del operador.
En resumen: Aunque el robot en sí es un dispositivo complejo, en esta aplicación simplifica el sistema completo, haciéndolo más robusto y fácil de operar.
¿Nos puede contar más sobre la posibilidad de operar un turno sin personal con este sistema?
Con gusto. Ésta es justamente una de las principales ventajas de nuestro sistema con carga directa mediante robot. Con esta solución es posible operar lo que llamamos un “turno fantasma”, es decir, una producción completamente sin personal durante toda una jornada. Para lograrlo, utilizamos ya sea una celda de apilado tipo CRC o una celda tipo SCS. Estas celdas están diseñadas para almacenar una gran cantidad de piezas en bruto. El robot accede de forma autónoma a estas piezas y se encarga de todo el proceso de carga y descarga, sin necesidad de intervención humana.
El resultado es un aumento significativo en la eficiencia general del sistema (OEE). Imagínese: la máquina puede operar durante toda la noche, los fines de semana o incluso en días festivos —siempre—, sin que haya operadores en sitio. Esto incrementa la productividad de forma considerable, sin aumentar los costos de personal.
Otro beneficio importante es la constancia en la producción. El robot trabaja siempre con la misma velocidad y precisión, ya sean las 2 de la madrugada o las 2 de la tarde. Esto garantiza una calidad muy uniforme en las piezas fabricadas.
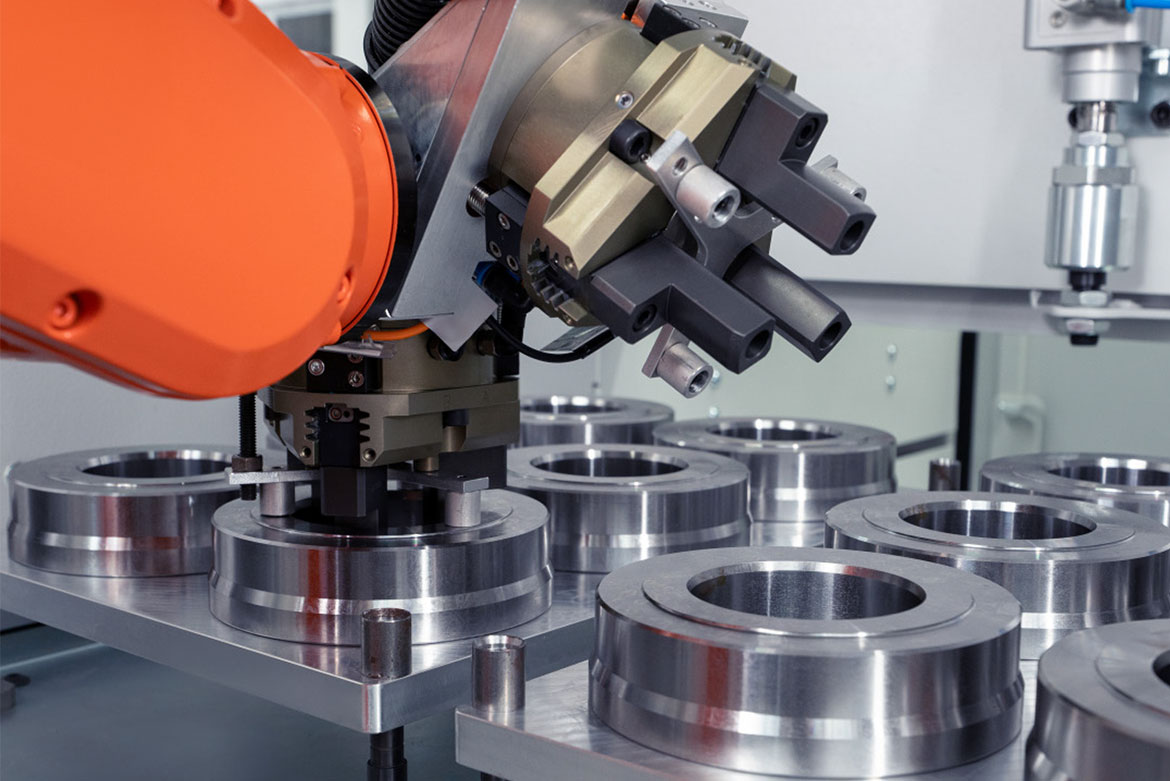
La celda de apilado CRC permite una producción totalmente automatizada.
Suena impresionante. Pero, ¿cómo aseguran que las herramientas sean suficientes para todo un turno?
Esa es una muy buena pregunta, ya que la vida útil de las herramientas suele ser uno de los factores limitantes en procesos de producción largos y sin personal. Aquí es donde entra en juego nuestra torreta de herramientas con capacidad para 12 posiciones, el cual desempeña un papel clave en este sistema.
La torreta de 12 posiciones nos permite trabajar con herramientas hermanas. Es decir, podemos cargar varias herramientas idénticas o muy similares en la misma torreta. Cuando una herramienta alcanza su vida útil, el sistema cambia automáticamente a la siguiente herramienta hermana.
Déjeme darle un ejemplo para ilustrarlo: supongamos que un proceso de mecanizado requiere cuatro herramientas diferentes. En un sistema convencional, esas cuatro herramientas determinarían el tiempo máximo de operación. Con nuestra torreta de 12 posiciones, podemos cargar cada una de esas herramientas tres veces. Esto triplica efectivamente el tiempo de operación posible sin necesidad de cambiar herramientas.
Adicionalmente, utilizamos sistemas avanzados de monitoreo de desgaste. Estos sistemas supervisan de forma continua el estado de las herramientas y pueden predecir con precisión cuándo es necesario un cambio. Así garantizamos un uso óptimo de las herramientas hermanas y evitamos interrupciones inesperadas en la producción debido a fallas.
Esta combinación de alta capacidad de herramientas y una gestión inteligente de las mismas nos permite producir durante todo un turno —ya sea de 8, 10 o incluso 12 horas— sin necesidad de personal. Y eso es clave para lograr turnos sin operador realmente eficientes.
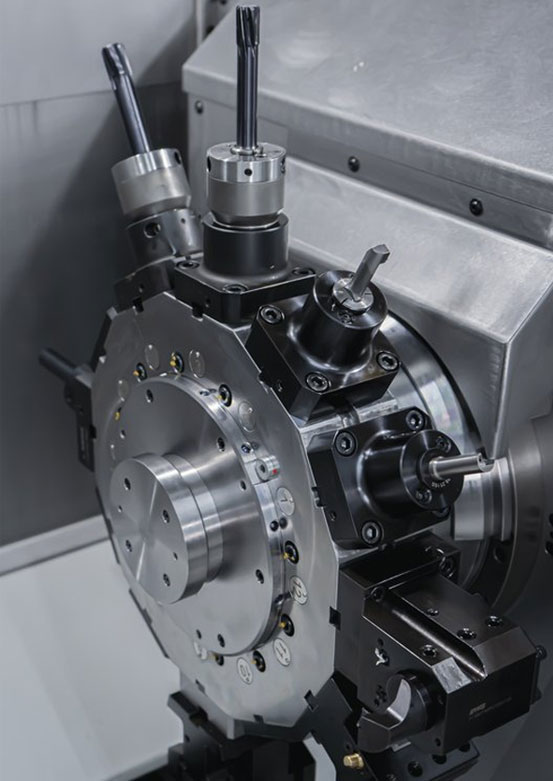
Toma en primer plano de la torreta de herramientas de 12 posiciones, que aloja diferentes herramientas para la producción sin personal.
Parece un sistema muy bien pensado. ¿Qué beneficios concretos ofrece a los clientes?
Los beneficios para nuestros clientes son múltiples:
- Mayor productividad: Al poder producir 24/7, nuestros clientes pueden aumentar significativamente la utilización de sus equipos y, con ello, su producción total.
- Rentabilidad: Los turnos sin personal reducen de forma notable el costo por pieza producida.
- Flexibilidad: El sistema puede cubrir fácilmente turnos de noche, fines de semana o días festivos sin necesidad de asignar personal adicional.
- Calidad constante: Nuestras máquinas y el robot trabajan siempre con la misma precisión, lo que garantiza una calidad constante de las piezas.
- Uso optimizado de recursos: el uso inteligente de la torreta de 12 posiciones y el uso de herramientas hermanas, se aprovecha al máximo la vida útil de cada herramienta.
- Menor carga de planificación: Una vez configurado, el sistema puede ejecutar largos ciclos de producción sin requerir supervisión constante.
- Ventaja competitiva: La capacidad de producir de forma flexible y rentable puede marcar una gran diferencia en sectores con alta competencia.
En resumen, nuestro sistema permite a nuestros clientes optimizar su producción, reducir costos y, al mismo tiempo, aumentar su flexibilidad y capacidad de respuesta a las demandas del mercado.