En el mundo de las máquinas herramienta, la optimización del diseño de los procesos es crucial para alcanzar la máxima precisión y eficiencia. En nuestro artículo del blog de hoy, hablamos con Jörg Lohmann, Director de Tecnología y Gestión de Productos, además de miembro de la Junta Directiva de EMAG Koepfer, paraconocer más sobre el diseño de los procesos de fresado de engranes, utilizando como ejemplo engranes planetarios. Jörg Lohmann cuenta con casi 20 años de experiencia en el desarrollo y aplicación de fresadoras de engranes y procesos de fresado de engranes, y nos ofrece una visión más profunda de la toma de decisiones que hay detrás de estos procesos.
Señor Lohmann, ¿qué es lo que, en su opinión, distingue especialmente a EMAG Koepfer?
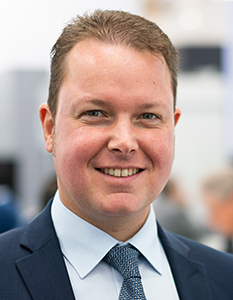
Jörg Lohmann, Director de Tecnología y Gestión de Productos y miembro del Consejo de Administración de EMAG Koepfer
No es tan fácil de responder. EMAG Koepfer es una empresa muy familiar, donde prácticamente todos se conocen. Esta combinación de compañerismo, conocimientos y experiencia hace que, después de tantos años, me siga gustando venir a trabajar. Creo que nuestros clientes también lo perciben así. Reciben un servicio de asesoramiento y apoyo personalizado y competente para cada proyecto y pueden estar seguros de que sus preocupaciones se tomarán en serio. Además, al formar parte del grupo EMAG podemos adaptarnos de maneramuy especifica a las necesidades de los clientes, por ejemplo para realizar procesos de fabricación complejos, hasta sistemas de fabricación llave en mano. De este modo, EMAG Koepfer ofrece una combinación única de contacto personal, conocimientos técnicos y una gran experiencia. Todas estas características hacen que la empresa y nuestras soluciones sean realmente especiales.
La experiencia también es importante cuando se trata del tema que hoy nos ocupa, el diseño de procesos de fresado. ¿Cómo abordan esto exactamente?
Sí, la experiencia es esencial, pero primero es necesario comprender y dominar por completo los aspectos técnico-físicos de esta tecnología compleja. Esto requiere un profundo entendimiento matemático, complementado con conocimientos generales sobre procesos de mecanizado. Cuando esto se cumple, como es el caso de EMAG Koepfer, me atrevería a decir que la experiencia es el recurso más importante en el desarrollo de procesos de engranajes. Pero ahora me estoy adelantando. Para poder describir todo el proceso de desarrollo de forma más clara, me gustaría explicarlo con un ejemplo. Los engranes planetarios. En este caso, se requieren altos estándares de calidad para el producto final, que además debe fabricarse en grandes cantidades.
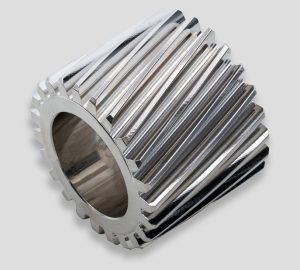
Con esta tecnología, el corte de engranajes planetarios puede realizarse en un tiempo ciclo inferior a 8,5 segundos. Esta producción rápida y eficaz es un factor importante para la competitividad en la industria del automóvil.
El diseño suele comenzar con la recepción del plano de la pieza y la hoja de especificaciones del cliente, que establece los parámetros iniciales, como los requisitos para los procesos previos y posteriores, la clase de calidad tras el mecanizado del engranaje, las cantidades deseadas, etc. Esta información constituye la base para los diseños de un proceso de mecanizado. Hay un gran número de factores que deben tenerse en cuenta e innumerables posibilidades para el diseño del proceso. Y aquí es precisamente donde entra en juego nuestra experiencia, ya que podemos descartar muchos procesos menos eficaces en una fase muy temprana. A partir de ahí, se realiza un cálculo de variantes y se comparan distintas variantes de proceso para determinar la solución más económica.
¿Cuál es la primera pregunta que usted se hace?
En primer lugar, hay que saber qué aspecto debe tener el componente acabado. De ahí se deriva toda la cadena de procesos y los requisitos que debe cumplir el mecanizado de engranes. Después, se consideran otros aspectos, por ejemplo, si utilizamos la mecanización en húmedo o en seco. La mecanización en seco suele ser más eficiente, sobre todo para grandes volúmenes. Esto permite trabajar con mayores parámetros de corte y eliminar pasos como el lavado antes del temple. De este modo, se puede reducir la manipulación de las piezas de trabajo y el plazo de entrega. De esta manera, el proceso en seco ofrece muchas ventajas, pero también plantea grandes exigencias. Por un lado, se necesita la máquina adecuada con el rendimiento y la precisión necesarios y, por otro, un determinado número de piezas para poder ejecutar el proceso a la perfección. Aquí es donde vuelve a entrar en juego la experiencia, que es sencillamente necesaria para perfeccionar este proceso. Afortunadamente, en EMAG Koepfer cumplimos con todos estos requisitos – naturalmente también para nuestra pieza de ejemplo “engranes planetarios”, para la que ya hemos suministrado innumerables máquinas en todo el mundo.
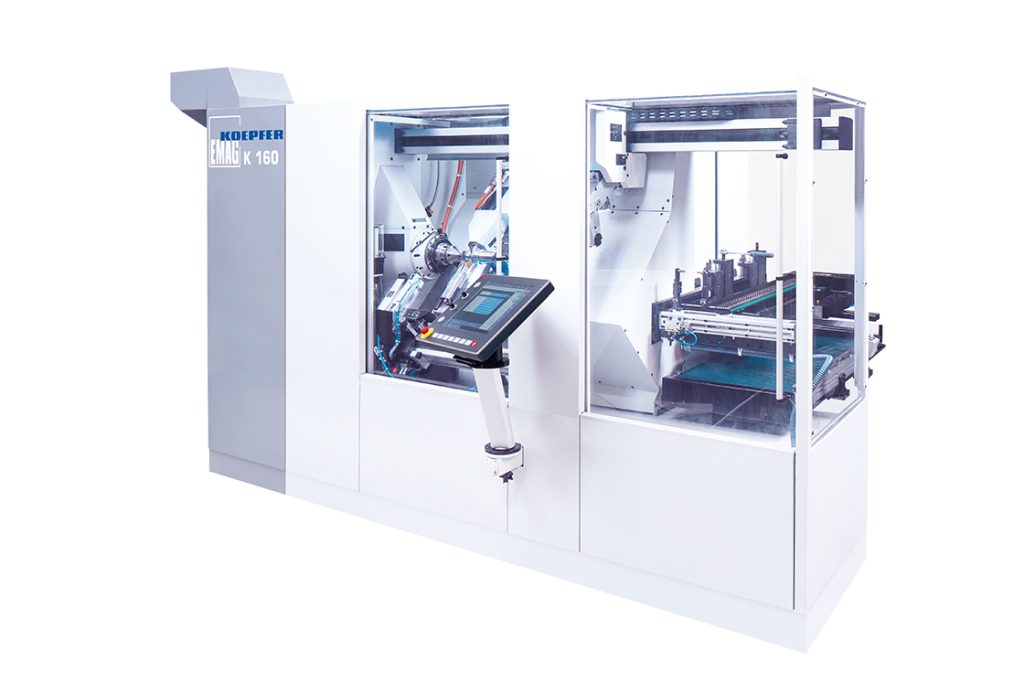
La K 160 es una máquina de tallado de engranajes universal y multifuncional que puede producir eficazmente diversos tipos de engranajes. Esto incluye el tallado de engranajes frontales, la producción de engranajes de tornillo sin fin, engranajes cónicos de dentado recto mediante el proceso Conikron y la producción de engranajes espiroidales.
Qué hay que considerar en el tema de las herramientas?
Además de la máquina, el diseño de la fresa de corte, por supuesto, el criterio decisivo en el proceso de fresado, ya que tanto su diseño como los parámetros de corte elegidos se influyen mutuamente. Aquí surgen preguntas como: ¿De qué material debe estar hecho el cortador de la fresadora? ¿Se debe elegir un cortador de vástago o uno de agujero? ¿Cuántas entradas debe tener el cortador? Y muchas más. Todo esto influye a su vez en los posibles parámetros de corte y también en la calidad de los engranes producidos. Con esto ya nos adentramos bastante en el diseño del proceso de fresado, ya que cada decisión que se toma aquí también repercute al final en los costos. Un cortador de vástago es más caro que uno de agujero, pero puede tener mayor longitud y, por lo tanto, mecanizar más piezas antes denecesitar ser afilado nuevamente. El tiempo de mecanizado y la calidad del engrane producido dependen del diseño del cortador y de los parámetros de corte utilizados. Como ya he dicho, básicamente todo aquí es interconectado y no hay otra obción más que probar diferentes condiguraciónes.
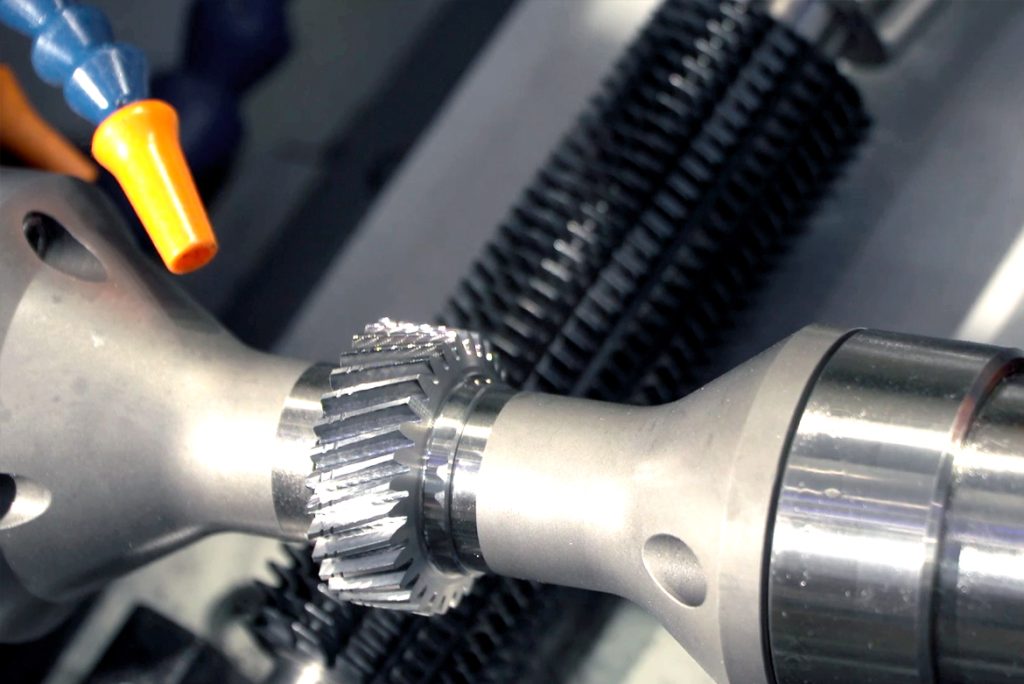
Para fabricar un engranaje planetario para una caja de cambios automática de un coche se utiliza un proceso de corte en seco con fresas multiarranque de metal duro. Con esta tecnología, el corte de engranajes planetarios puede realizarse en un tiempo ciclo inferior a 8,5 segundos. Esta producción rápida y eficaz es un factor importante para la competitividad en la industria del automóvil.
¿Cómo puede imaginarse esta prueba y error?
Bueno, por supuesto no probamos los distintos diseños en la realidad, sino que utilizamos software de simulación para este paso del proceso. Pero aquí también tengo que remitirme a la experiencia, porque podemos echar la vista atrás a muchos años de diseño de procesos y, por supuesto, ya sabemos qué valores tienen sentido para empezar. Todo lo que viene después es básicamente la búsqueda de la relación óptima entre coste y calidad. En otras palabras, buscamos el proceso de mecanizado en el que podemos producir las cantidades necesarias con la calidad deseada a los costes unitarios más bajos. Este es el proceso de mecanizado óptimo. En nuestro ejemplo, esto significa que podemos mecanizar un engranaje planetarios de este tipo en menos de nueve segundos, al menos en lo que se refiere al mecanizado suave: el engranaje planetario primero se fresa previamente y luego se templa y, a continuación, debe mecanizarse con precisión. Pero entrar en más detalles iría más allá del alcance de este artículo. Por ello, me gustaría aprovechar esta oportunidad para remitirle a nuestro seminario web, en el que explico todo el proceso en detalle.
Señor Lohmann, gracias por la entrevista.