09/01/2024 - Oliver Hagenlocher - Press
Solutions de rectification d'EMAG SU : Une qualité de surface extrême pour l'e-mobilité
Une précision et une sécurité particulières des processus caractérisent la construction automobile depuis de nombreuses décennies. Avec l'avènement de l'e-mobilité, ces exigences augmentent encore, car de nombreux composants de moteurs électriques doivent être fabriqués de manière encore plus "parfaite" : La plupart du temps, il s'agit d'obtenir une qualité de surface maximale de l'ordre du micromètre afin d'éviter, par exemple, que les composants de la denture ne génèrent des bruits de fonctionnement - étant donné que le moteur électrique est silencieux, ces bruits deviendraient audibles. Dans ce contexte, la technologie d'EMAG SU est actuellement au centre de l'attention de nombreux planificateurs de production : nos spécialistes développent entre autres des solutions haute performance pour la rectification des dentures - y compris des temps de copeaux à copeaux courts, des concepts d'axes intelligents, une stabilité thermique et mécanique ainsi qu'une grande facilité d'utilisation. Quels sont les machines et les procédés qui retiennent l'attention ?
Images
Les machines G 250 d'une part et G 160 d'autre part constituent des solutions exceptionnelles dans le domaine de la rectification d'engrenages. La G 160 est utilisée pour des pièces jusqu'au module trois et avec un diamètre extérieur maximal de 160 millimètres. Dans ce domaine d'application, elle est la machine la plus rapide du marché, ce qui est rendu possible par deux tables porte-pièce parallèles qui se déplacent alternativement à grande vitesse vers la meule. Ainsi, pendant qu'une pièce est usinée, le robot de chargement interne insère une ébauche dans l'autre broche et décharge auparavant la pièce finie. En outre, le concept d'axe assure des surfaces parfaites, si importantes dans le domaine de l'e-mobilité. L'élément décisif est que la G 160 n'a pas d'axe tangentiel, mais que les axes Y et Z existants créent un axe tangentiel "virtuel" par un mouvement simultané. En conséquence, la distance entre l'axe A et le point de contact de l'outil est très faible, ce qui évite à son tour les "fréquences fantômes" sur la surface de la pièce. L'exemple d'un "arbre intermédiaire" avec 21 dents et un module normal montre les possibilités offertes par cette approche pour l'électromobilité, avec un temps à la pièce de seulement 33 secondes (y compris le phasage denture et le temps de dressage proportionnel) et un temps de rectification de seulement 25 secondes. Des valeurs de performance similaires sont obtenues avec un arbre d'entrée de 26 dents et un module de 1,6 millimètres. Ici, le temps de rectification pur n'est que de 28 secondes.
Temps minimal à la pièce
La machine G 250, plus grande, marque également des points avec sa précision, ses temps de copeaux à copeaux minimaux, ses temps de préparation courts et sa fiabilité pour les pièces d'une longueur maximale de 550 millimètres. La machine est également équipée d'une double table (comme la G 160). Les opérations de chargement et de déchargement ainsi que la mesure des composants sont donc effectuées en temps masqué. Autre point intéressant : le mandrin de rectification peut recevoir des meules de différents diamètres et l'ensemble de la construction est très rigide. La rectification par génération et la rectification de profil ont lieu sur la broche de rectification principale, de sorte que la machine n'a pas de dilatation thermique. De plus, elle peut être transformée en quelques minutes d’un procédé à l’autre. Dans le domaine de l'e-mobilité, cette approche est utilisée par exemple pour la rectification des roues motrices des essieux. Le temps à la pièce n'est que de 69 secondes (y compris la compensation de l’indexage et le temps de dressage proportionnel), le temps de rectification proprement dit n'étant lui-même que de 58 secondes. La G 250 atteint une productivité élevée comparable lors de l'usinage de pignons avec une forte courbure dans le profil des flancs de dents et une courbure normale dans la ligne des flancs. Le temps à la pièce est de 33 secondes et le temps de rectification pur de 28 secondes. On obtient une qualité DIN-3962 de 4.
Sky Grind : Réduire massivement les coûts
En outre, EMAG SU illustre l'avenir général de la rectification d'engrenages avec la mise en place du nouveau procédé "Sky Grind". Ici, la rectification finale de la roue dentée est réalisée entièrement à sec - avec de gros avantages économiques pour les utilisateurs, car l'installation de la filtration, du refroidisseur et autres (normalement nécessaires pour la rectification sous arrosage) sont supprimés, ce qui réduit l'investissement initial. De plus, la consommation d'énergie est massivement réduite. Tout cela est rendu possible grâce à un système Dual-Tool avec deux broches d'outils différentes dans la machine : une pour la semi-finition par taillage et une pour la finition par rectification. En pratique, cela signifie que, par exemple, dans le cas pignon automobile classique avec une surépaisseur de 100 µm par flanc, le procédé Sky-Grind permet d'enlever 90 microns par le taillage par génération et seulement 10 microns par la rectification par génération. Au final, les temps de cycle de la rectification conventionnelle sous arrosage des engrenages et du procédé Sky-Grind sont très similaires - mais les coûts sont très différents.
Comment peut-on résumer le savoir-faire et l'offre d'EMAG SU ? "On pourrait certainement dire que nous garantissons à nos clients des avantages concurrentiels et un "retour sur investissement" rapide", répond Alexander Morhard d'EMAG SU. "Pour cela, nous investissons en permanence dans la recherche et le développement afin d'améliorer encore l'efficacité et le respect de l'environnement de nos machines. Au final, nous obtenons des solutions parfaites pour la réalisation de surfaces très fines avec différents contours".
Interlocuteurs
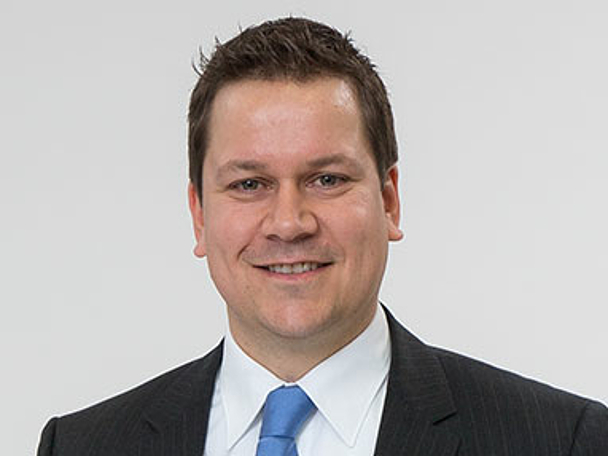