Manufacturing System for Sprocket Machining
With the vertical pick-up turning centers of VL-Series and a VL 4 H vertical hobbing machine, EMAG offers the ideal manufacturing systems for the complete machining of sprockets. An EMAG TrackMotion system is added to the system, which transports the parts smoothly between the machines, and will also flip the sprockets over when needed or deposit them on to stacker pallets.
Ideal Manufacturing Systems for the complete machining of Sprockets
Modular machines are perfect for the use in a wide variety of manufacturing scenarios. Their integrated automation and the consistent transfer height between the machines allow for the use of a wide range of automation solutions without the need for an expensive gantry or robot solution. In this sprocket manufacturing solution, the focus is on maximizing the ease of handling for the operator. Although the loading of the machine is effortless, due to the integrated automation and raw-part storage, the use of a separator provides even more freedom. With this solution you have the choice of either letting the cut raw-parts drop directly into the separator, or of transferring them between the saw and the production line on pallets. The highly efficient EMAG production system ensures tidy stacking of the sprockets, which is ideal for further processing. Easy handling combined with maximum productivity and precision of production—another state-of-the-art manufacturing solution developed by EMAG.
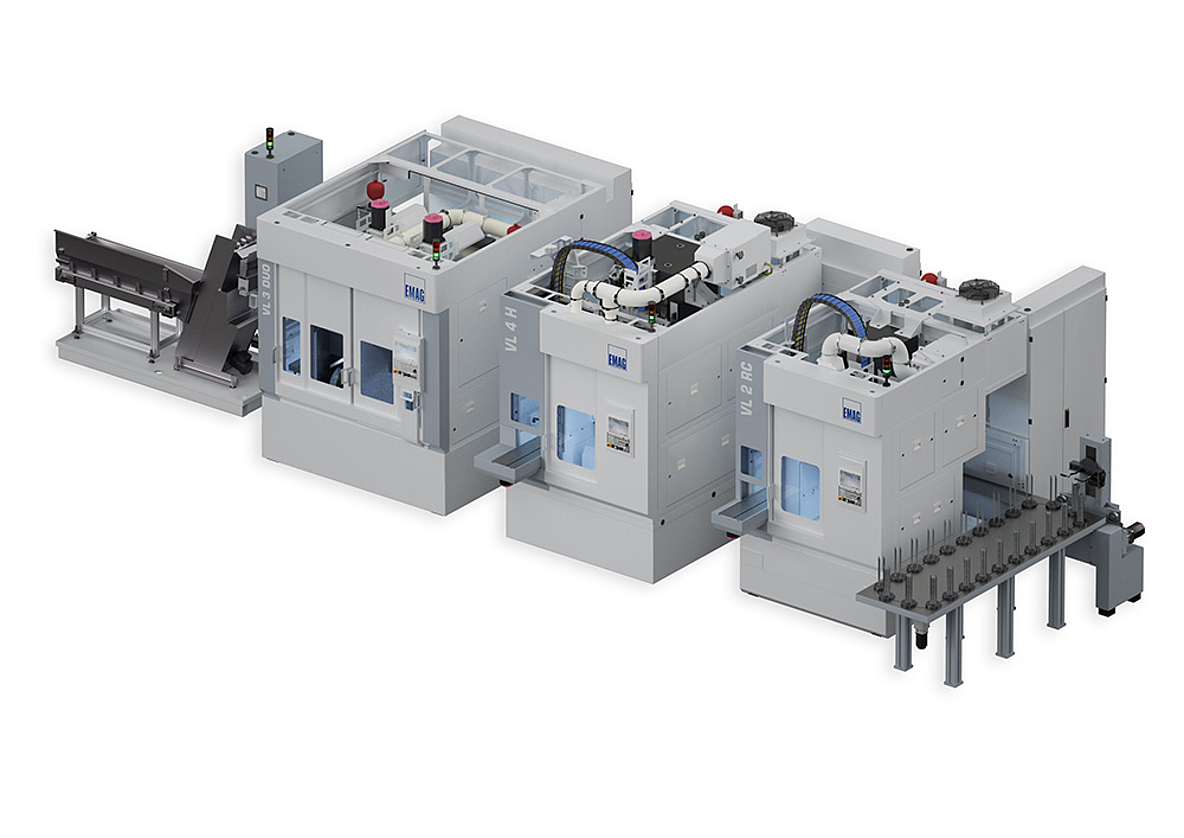
OP 10 – OP 40
OP 10 / OP 20: VL 3 DUO – Highly efficient production in just 24.5 m²
Advantages of the VL 3 DUO
- Fast automation: OP 10 + OP 20 machining with workpiece handling and flipping in just 23 sec.
- With a minimum machining time of 15 seconds, machining idle times have been nearly eliminated.
- Parts storage for up to 400 parts
OP 30: VL 4 H – the fastest pick-up hobbing machine in the world
The advantages of the VL 4 H
- High-speed pick-up hobbing machine for hobbing chucked parts with tailstock
- Optimum chip flow – ideal for high-performance dry hobbing
- Measuring probe for post-process measurement with optional process stabilization
- Tailstock for optimum stability and maximum tool life
OP 40: VL 2 RC – Outstanding production-line chamfering
The advantages of the VL 2 RC
- Chamfering in the production line – parts don't travel far
- Separate or downstream chamfering, preventing time loss during hobbing
- Greatest possible reduction in secondary burring and material accumulation

The pick-up turning centers in the VL series for sprocket machining
The vertical pick-up turning centers in the VL series are an example of a new machine concept from the EMAG Group – the modular machines.
The vertical pick-up turning centers of the VL series were developed specificallyfor the production of precision chucked parts, such as sprockets. There are four versions of the VL machine to cover the widest possible range of parts, from 10 mm up to 400 mm in diameter.
The advantages
- Fully vertical model families with modular design
- Ideal for mass production – from small to high batch sizes
- Every machine includes all the automation and handling systems required
- Automation of multiple machines is easy
- Perfect for operation of multiple machines by one person
More information about the VL-Series
VL 4 H – Modular gear-cutting machine for sprocket production
High-productivity cutting of gear teeth – the VL 4 H hobbing machine.
The VL 4 H features high-performance drives that enable high speeds and torques on the working spindle and the hob. These systems ensure the productive manufacture of sprockets with a diameter of up to 200 millimeters and module 4, by means of dry hobbing with a short process time.
The machine's Mineralit® base ensures low-vibration machining of the workpieces and contributes to the machine's excellent machining quality. The vertical structure of the machine with pick-up spindle keeps non-productive time to a minimum, as there are only a few seconds between setting down the finished part and picking up the raw part and transporting it to the cutting head.
The pick-up automation system also permits the use of a measuring probe, which is positioned outside the machining area, where it is optimally protected from contamination.
The advantages
- High-speed pick-up gear hobbing machine for hobbing chucked parts with tailstock
- Optimum chip flow – ideal for high-performance dry hobbing
- Measuring probe for measuring the cut teeth, and sensor system for alignment with holes or grooves. Both the measuring probe and the sensor system are fitted outside the machining area, for optimum protection from chips and dirt
- Easy integration into manufacturing systems
- Integrated automation: no additional costs
- Proven KOEPFER gear hobbing technology
- Both Fanuc and Siemens (VLC 200 H) controls possible
More information about the VL 4 H
Technologies
Complex Manufacturing Systems from a Single Source thanks to a High Range of Technologies
Vertical turning is a machining process for metal components. EMAG was one of the first machine tool manufacturers to use the vertical turning process…
Machines for your requirements
(1) machines found