19/01/2021 - Oliver Hagenlocher - Customer Stories
Interprecise Donath GmbH à Fürth : En quoi la production de roulements à rouleaux de précision profite aux machines EMAG
De nombreuses machines et réducteurs sont inconcevables sans roulements à rouleaux. Leur conception circulaire facilite les mouvements de roulement et réduit la friction. Leur production exige toutefois une précision extrême de l’ordre du micromètre – une mission à la hauteur de l’entreprise Interprecise Donath Gmbh, qui a son siège à Fürth : depuis plus de 30 ans, cette entreprise fabrique des roulements à rouleaux particulièrement exigeants, comme pour la construction de machines ou de réducteurs. La planification, la conception et la production sont entièrement réalisées en interne. Utilisés depuis 2017 : les centres de tournage VL verticaux d’EMAG. Avec une automation pick-up intégrée, ils permettent d’augmenter la productivité et garantissent dans le même temps la qualité requise pour l’usinage doux et dur pour des composants tels que des bagues de roulement. Quelle expérience les spécialistes des roulements ont-ils acquise avec cette solution de production ?
Images
Dans quelles applications ne trouve-t-on pas de paliers ? La question se pose, car ces composants se trouvent en effet dans de très nombreuses machines, réducteurs et véhicules. Généralement montés sur des arbres ou des axes, ils servent ici au guidage ou à la transmission de charges : cela nécessite une très faible friction afin de réduire la consommation énergétique de l’entraînement. Un contexte d’utilisation, qui laisse déjà supposer quelles difficultés, implique leur fabrication : il s’agit de tolérances de fabrication de l’ordre de quelques micromètres, garanties par des experts en roulements tels que Interprecise Donath GmbH. Avec ses quelques 140 employés et un chiffre d’affaires d’un peu moins de 27 millions d’euros, l’entreprise qui a son siège en Bavière évolue dans une « niche de qualité » particulière, ainsi que le souligne le directeur Christian Witte : « Nous nous concentrons sur les applications spéciales pour lesquelles nos clients n’ont besoin que de petites quantités, entre un et 2 000 exemplaires. On peut parler d’un segment de marché de haute précision, qui ne permet pas de fabrication en série sans personnel. Au contraire, nous comptons sur le travail de chacun : des spécialistes qualifiés surveillent le processus dans les machines et contrôlent en permanence la qualité finale des différentes pièces à l’aide de techniques de mesure. Notre tolérance aux erreurs est nulle. »
Faire face avec efficacité au nombre croissant des commandes
Et ce n’est pas tout : Interprecise se positionne sur le marché comme un acteur extrêmement rapide et flexible. Chaque demande d’un nouveau roulement est traitée directement et sans délai. La mise en œuvre de la conception avec les dessins techniques démarre également à plein régime. « Notre réactivité et l’assistance complète que nous fournissons de bout en bout à nos clients, dans ce domaine technique exigeant, sont indéniablement nos atouts, » souligne M. Witte. Une stratégie qui a mené l’entreprise sur la voie d’une croissance constante : le nombre de salariés a presque triplé au cours des seules 13 dernières années. L’année 2007 a une signification particulière, puisqu’il s’agit de l’année où pour la première fois nos spécialistes ont utilisé la marque « iDC », apposant pour la première fois un nom sur la qualité de nos roulements. Il y a trois ans, cependant, cette évolution a confronté les planificateurs d’Interprecise à une question essentielle : comment produire un nombre croissant de variantes et de familles de composants de la manière la plus rentable possible sans pour autant que les process ne perdent en précision et en fiabilité ? M. Witte a trouvé la réponse en observant l’automation pick-up des machines verticales EMAG : « J’ai d’abord étudié cette solution avec nos clients. Le fonctionnement de cette machine, qui est chargée automatiquement par la broche principale et peut donc fonctionner de manière partiellement automatisée, convenait parfaitement à nos applications. Cela nous permet d’augmenter la productivité, même sur de petites quantités, car un opérateur peut facilement superviser plusieurs machines. En définitive, cela signifie que nous pouvons produire davantage avec le même nombre de collaborateurs ». En 2017, Interprecise a investi dans ses deux premiers postes pick-up VL 4, rejoints un an plus tard par un VL 4 et un VL 6 (pour les composants un peu plus grands). Par exemple, les bagues intérieures et extérieures des roulements sont soumises à un usinage « doux » puis à un usinage « dur » sur les quatre machines EMAG, mais au total, ce sont jusqu’à 50 composants différents qui sont usinés dans les machines VL. Le nombre de pièces par lot varie entre cinquante et cinq cents. Les spécialistes effectuent un nouveau réglage des centres de tournage pick-up environ trois fois par semaine.
Des coûts unitaires réduits avec la solution EMAG
Interprecise se dit particulièrement satisfait de cette solution, comme l’explique Daniel Braun, en charge de la préparation du travail et de la programmation. « Au final nous avons pu réduire les coûts unitaires de manière significative, d’environ 15 %, car les machines fonctionnent sans problème en mode autonome. L’ensemble de notre processus de production bénéficie de manière déterminante de la construction des machines ». La séquence est très simple : l’opérateur place le composant sur l’un des anneaux d’entraînement du convoyeur et le récupère au même endroit. Le tapis permet un stockage intégré des pièces et la machine peut produire sans surveillance pendant une longue période. Le process qui se déroule à l’intérieur de la machine est très efficace : la broche pick-up retire les composants du cadre d’entraînement et les achemine à grande vitesse vers l’espace de travail et sa tourelle porte-outils intégrée à 12 positions. Les courtes distances assurent des temps de copeau à copeau tout aussi courts. Une fois le premier côté fini (et la pièce évacuée par le tapis vers l’extérieur), l’opérateur ne doit apporter que des réglages minimes à la machine. Il suffit ensuite de replacer les pièces retournées sur le convoyeur pour usiner le deuxième côté. La station de mesure intégrée entre l’espace de travail et le poste pick-up joue un rôle important, car elle permet de mesurer la pièce avant le chargement et le déchargement. En fonction du résultat de la mesure, la machine se réajuste automatiquement, corrige ainsi l’usure de l’outil et assure la précision de répétition indispensable pour la fabrication de haute précision des bagues de roulement.
Priorité à la flexibilité
La conception globale des machines VL est tout aussi importante en terme de précision et d’économie. Le bâti de la machine en béton polymère Mineralit® réduit les vibrations pendant le process d’usinage et garantit une longue durée de vie de l’outil et une haute qualité de l’état de surface. De plus, la broche principale est fixée à l’avant par un chariot transversal et permet un mouvement dynamique dans les axes X et Z. En outre, les opérateurs bénéficient de la bonne accessibilité de l’espace de travail et de la tourelle outils. Le tour vertical peut donc être rééquipé en peu de temps. « C’est un critère important pour nous, déclare M. Braun. Nos atouts sont notre réactivité et nos délais de livraison rapides, et ceux-ci dépendent en fin de compte de la flexibilité de la production sur commande. La modification des réglages des machines doit donc être très rapide et s’effectuer simplement. Avec une solution EMAG, c’est tout à fait garanti. »
Les machines EMAG : une base importante pour la production
Pour finir, reste à savoir dans quelle direction se développe la technologie des roulements à rouleaux et dans quelle mesure cela aura une influence sur la solution de production. Dans ce contexte, Daniel Braun évoque les exigences de qualité croissantes, comme dans la construction mécanique, où les roulements à rouleaux Interprecise sont utilisés en grand nombre : « Prenons par exemple les presses à imprimer. Il est évident que les exigences en matière de qualité d’impression sont en constante augmentation, et celle-ci dépend notamment de la précision mécanique des machines utilisées. Les roulements à rouleaux utilisés sont décisifs à cet égard. Ils doivent donc être fabriqués avec une précision maximale et s’user le moins possible, et c’est précisément ce que nous rendons possible grâce à notre savoir-faire en matière de développement et de production. Les choses sont similaires dans de nombreux domaines d’application. Pour cela, les machines EMAG constituent une base de production importante. Nous sommes donc parfaitement équipés. »
Téléchargements
Interlocuteurs
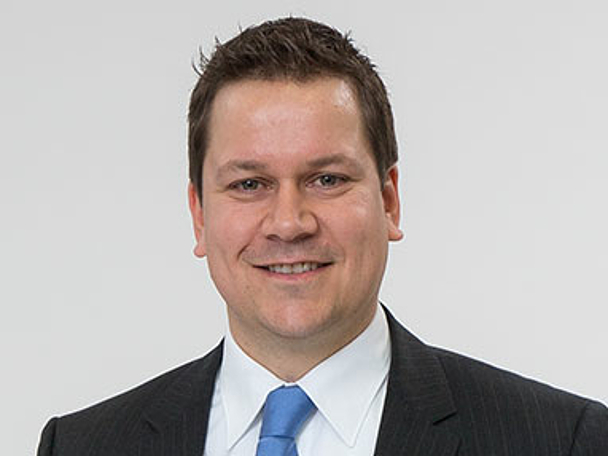
Oliver Hagenlocher
Zone
Press and Communication