Energieeffizienz bei EMAG: Fokus auf effiziente Fertigungsverfahren
EMAG hat schon immer Wert auf Effizienz gelegt, was in der heutigen, von Klimawandel und Nachhaltigkeit geprägten Welt von großer Bedeutung ist. Dieses Engagement für Effizienz zeigte sich bereits in der Einführung der ersten Maschine mit kombinierter Dreh- und Schleiftechnologie im Jahr 1996, einem Meilenstein in der energieeffizienten Produktion. EMAG konzentriert sich kontinuierlich auf Innovation und den Einsatz effizienter Fertigungstechnologien, um den Anforderungen der modernen Fertigungsindustrie gerecht zu werden.
Mineralit-Guss
Das Mineralit-Gießverfahren zeichnet sich durch einen geringen Energieverbrauch aus. EMAG verwendet diesen Werkstoff für die Grundkörper seiner Maschinen, um die Steifigkeit zu erhöhen, Vibrationen zu reduzieren und damit die Bearbeitungsgenauigkeit zu verbessern. Der Einsatz von Mineralit trägt somit nicht nur zur Verbesserung der Produktqualität bei, sondern auch zur Energieeffizienz, da eine höhere Bearbeitungspräzision weniger Ausschuss und damit weniger Energieverbrauch bedeutet.
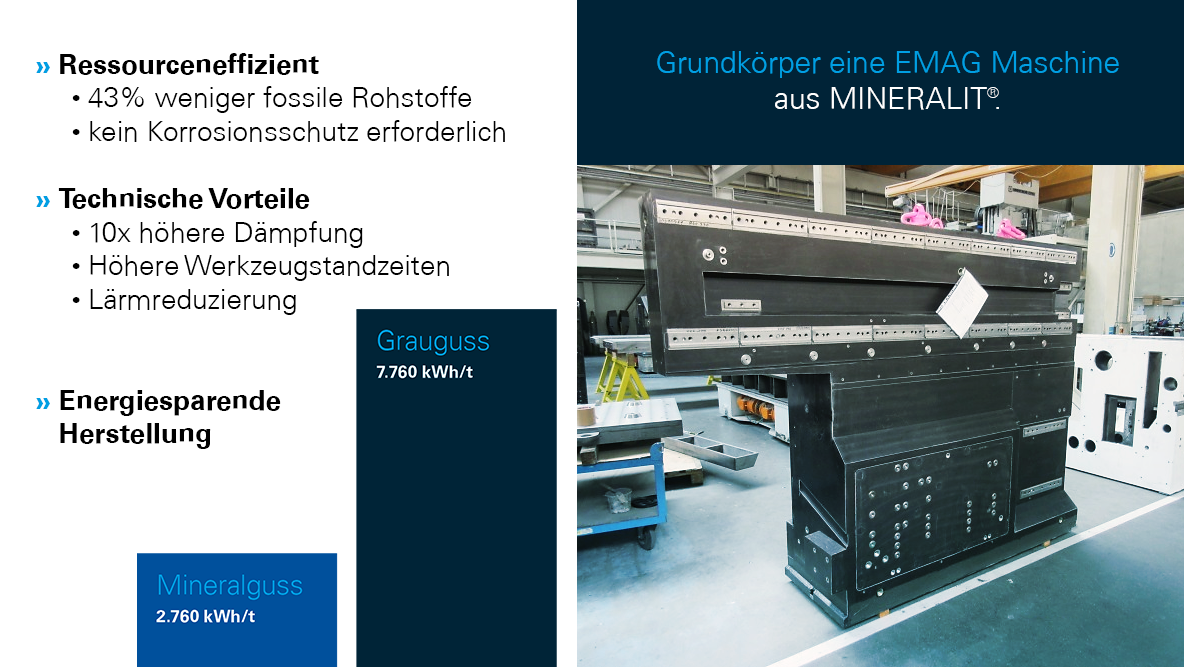
Vergleich zwischen der Herstellung von Mineralit und Stahlguss. Er zeigt die erheblichen Energieeinsparungen und somit Umweltfreundlichkeit, die durch den Einsatz von Mineralit erreicht werden.
Mineralit: Die umweltfreundliche Alternative
Bei der Energieeffizienz spielt die Wahl des geeigneten Fertigungsverfahrens eine entscheidende Rolle. Ein besonders anschauliches Beispiel ist die Herstellung der Grundkörper, die in EMAG Maschinen zum Einsatz kommen. Traditionell werden diese aus Stahl als Gussteil hergestellt; ein Prozess, der bei hohen Temperaturen abläuft und damit einen hohen Energieaufwand erfordert.
Eine effizientere und umweltfreundlichere Alternative ist die Verwendung von Mineralit, einem Mineralguss. Im Vergleich zur Stahlschmelze erfolgt die Herstellung von Mineralit bei Raumtemperatur und ähnelt eher dem Gießen von Beton. Dieser kühle Produktionsprozess führt zu einer beeindruckenden Energieeinsparung von über 60 % gegenüber der herkömmlichen Stahlgussproduktion.
Die Wahl des richtigen Produktionsverfahrens zu Beginn der Produktion führt also zu einer erheblichen Steigerung der Energieeffizienz.
Immer die effizienteste Lösung durch große technologische Bandbreite
Darüber hinaus bietet EMAG ein breites Spektrum an Fertigungstechnologien für die Maschinen an. So besteht die Möglichkeit, für jeden Kunden das beste Fertigungsverfahren auszuwählen – auch hinsichtlich der Energieeffizienz. Ein Beispiel hierfür ist der Vergleich der Verfahren Schleifen, Hartdrehen und Schäldrehen. Bei vielen Werkstücken und Anwendungen sind die Technologien Hartdrehen und Schäldrehen energieeffizienter als das Schleifen. Sie ermöglichen zudem eine hohe Oberflächengüte und Maßgenauigkeit, wodurch Nachbearbeitungsprozesse teilweise komplett entfallen können und somit der Energieverbrauch in der Fertigung deutlich reduziert werden kann.
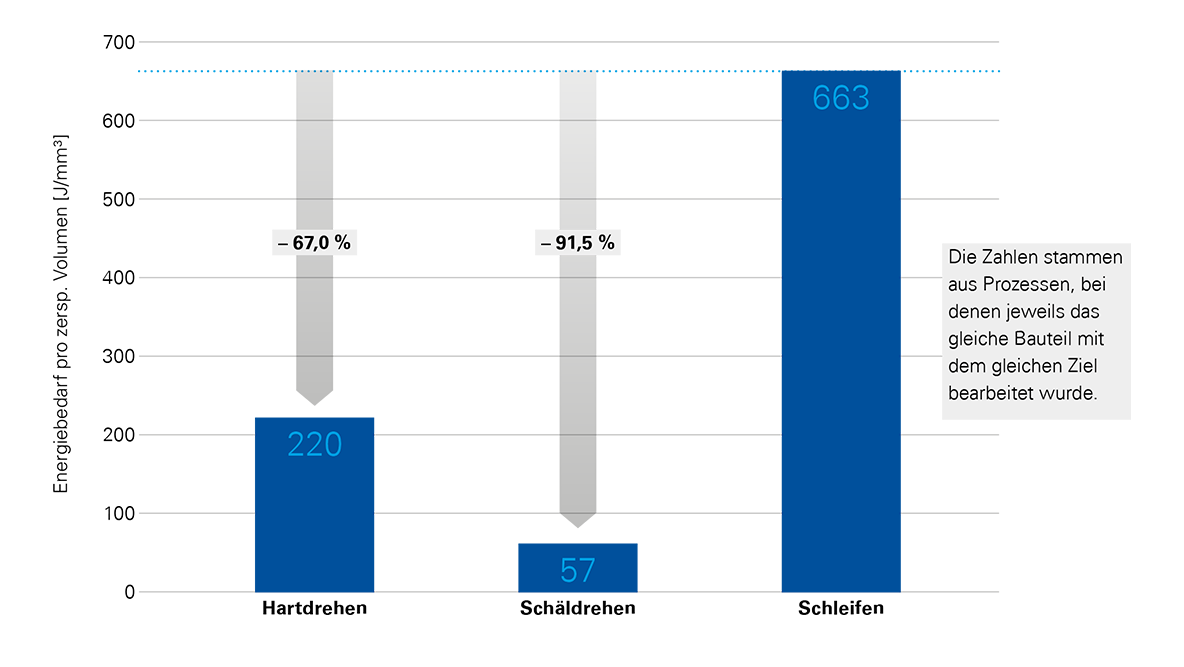
Eine Infografik zeigt den Vergleich zwischen Schleifen und Hartdrehen/Schäldrehen in Bezug auf Energieverbrauch und Bearbeitungszeit. Hervorgehoben wird der deutlich geringere Energieverbrauch und die kürzere Bearbeitungszeit beim Hartdrehen/Schäldrehen.
Schleifen vs. Hartdrehen/Schäldrehen: energieeffiziente Zerspanungsprozesse
Im Bereich der Zerspanung spielt die Wahl der richtigen Technologie eine entscheidende Rolle. Schleifmaschinen haben einen hohen Energiebedarf, bedingt durch die Schleifspindel, den Luftbedarf für die Öl-Luftschmierung sowie die Aufbereitung des Schmierstoffs. Eine Drehmaschine hingegen bietet energetische Vorteile. Vergleicht man das Schleifen und Hartdrehen des gleichen Bauteils, so zeigt sich, dass das Hartdrehen bzw. Schäldrehen eine Energieersparnis von bis zu 90 % ermöglicht. Zusätzlich verkürzt sich die Bearbeitungszeit erheblich. So konnte beispielsweise die Bearbeitungszeit bei einem Achszapfen von 15 Sekunden beim Schleifen auf nur 3 Sekunden beim Schäldrehen reduziert werden. Damit sinkt der Energiebedarf pro Werkstück immens.
Energieeffizienz ist für EMAG nicht nur ein Schlagwort, sondern integraler Bestandteil der Unternehmensphilosophie und Produktionsstrategie. Durch die Fokussierung auf effiziente Fertigungsprozesse trägt EMAG dazu bei, die industrielle Produktion effizienter und nachhaltiger zu gestalten und gleichzeitig die Wettbewerbsfähigkeit zu stärken.