01/12/2023 - Oliver Hagenlocher - Press
EMAG développe des solutions de fabrication globales : Des applications robotiques parfaitement adaptées garantissent un flux de pièces rapide dans la production
Les solutions de production avec automatisation robotisée ont le vent en poupe : elles permettent d'établir un flux de pièces rapide et à faible effectif au sein d'un site - et de réduire ainsi les coûts unitaires tout en augmentant la sécurité de production et la qualité. L'exemple d'EMAG montre comment un constructeur de machines aborde la tâche fondamentale de conception: les experts en production associent leur technologie de machine pick-up à des solutions robotisées très individuelles, conçues avec précision en fonction des exigences de la pièce et du processus de production. De quoi s'agit-il en détail ?
Images
Selon le rapport "World Robotics 2022" de la Fédération internationale de la robotique (IFR), environ 3,5 millions de robots sont désormais utilisés dans la production industrielle mondiale. L'Europe est le deuxième plus grand marché de la robotique au monde. Les exemples actuels d'EMAG montrent pourquoi il en est ainsi : les spécialistes combinent leurs machines haute performance avec des cellules robotisées très différentes - et assurent ainsi non seulement des processus hautement efficaces lors du chargement et du déchargement des machines, mais intègrent également des stations supplémentaires pour l'assurance qualité, le marquage, le nettoyage et bien d'autres choses encore. Mais quel est l'objectif général d'EMAG lorsque des robots sont utilisés ? "Les exigences de la pièce à usiner et du processus de production correspondant sont toujours au centre des préoccupations", explique Jürgen Maier, directeur de la Business Unit Tournage chez EMAG. "Les questions décisives sont par exemple la taille des lots à fabriquer dans une période donnée et le degré d'autonomie de la solution. Dans tous les cas, nous sommes très flexibles et nous nous adaptons de multiples façons à l'environnement de production existant ou à l'espace disponible".
Avec des tapis d'évacuation, des palettiseurs ou des tiroirs
Un coup d'œil sur les détails montre à quel point les solutions robotisées d'EMAG sont différentes : l'alimentation des pièces peut se faire par exemple par des bandes transporteuses, dans des palettes, sur des porte-pièces comme par exemple des paniers ou même en vrac - à l'aide de ces systèmes, le robot se "sert" lorsqu'il prend de nouvelles pièces ou les décharge terminées, chaque solution présentant des points forts et des conditions de base différents. Par exemple, les bandes transporteuses à tapis ou à rouleaux sont une variante idéale lorsque le flux de pièces doit s'effectuer sans problème d'une solution de production en amont vers la machine EMAG. Le robot peut alors facilement prélever les pièces sur la bande et les redéposer plus tard, les bandes étant agencées de différentes manières - en fonction de l'espace disponible ou du flux de pièces souhaité. Des butées pneumatiques assurent la séparation des pièces. Il est en outre possible de détecter l'orientation des pièces sur le tapis à l'aide d'une caméra. Lors du bin picking, ce que l'on appelle la "prise en caisse", les pièces brutes peuvent même être amenées de manière complètement chaotique, c'est-à-dire en vrac. Un système de caméra 3D détermine alors la position et l'orientation de chaque pièce à partir d'un nuage de points enregistré et calcule la stratégie d'approche optimale pour le robot. Cette technologie est donc parfaitement adaptée à une utilisation au tout début de la chaîne de création de valeur, car elle permet d'éviter complètement une pré orientation manuelle des pièces brutes.
À la différence, l'utilisation de palettiseurs suppose un démarrage "ordonné" : dans ce cas, le chargement et le déchargement du système se font par exemple via un chariot à paniers. Il contient des paniers grillagés empilés les uns sur les autres avec des nids de moulage correspondants, dans lesquels se trouvent les pièces - donc une quantité relativement importante par chariot, qu'un opérateur pousse simplement dans une position définie, et à partir de laquelle le robot peut y accéder. Le chariot avec les pièces finies se trouve à une autre position. "Pour une telle solution, il faut notamment mettre en relation le temps de cycle de la machine EMAG et les heures-hommes souhaitées sur la machine. Si la cadence d'usinage à l'intérieur de la machine n'est que de quelques secondes et que l'on souhaite en même temps un temps de manipulation minimal sur la machine, le concept d'automatisation peut être étendu par exemple avec notre unité d'empilage SCS 4 afin de maintenir l'autonomie de l'ensemble du système à un niveau élevé malgré des temps de cycle courts. Mais ce sont précisément les calculs que nous effectuons pour chaque solution robotique et que nous conseillons au client en conséquence", explique M. Maier.
Une troisième variante serait le chargement par système de tiroirs : dans ce cas, les pièces à usiner sont amenées dans des porte-pièces propres au client, via des tiroirs à entraînement pneumatique, dans la zone de travail du robot. Les tiroirs sont disposés les uns au-dessus des autres, ce qui permet d'obtenir un volume de stockage plus important et donc une plus grande autonomie pour la même empreinte au sol. Par ailleurs, le changement des porte-pièces par l'opérateur peut s'effectuer entièrement en temps masqué. Le robot peut ainsi continuer à travailler même lorsque la porte de chargement est ouverte, ce qui permet d'éviter les interruptions de la production.
Le nombre de solutions robotiques d'EMAG augmente
Pour toutes ces solutions, les possibilités d'équipement de chaque cellule robotisée sont importantes. Il est par exemple envisageable d'intégrer un contrôle statistique des processus (SPC). Dans le cas le plus simple, certaines pièces sont régulièrement retirées, mesurées et réintroduites dans la machine à des fins d'assurance qualité. En outre, la station de mesure elle-même peut être intégrée dans la cellule, de sorte que la mesure, y compris le retour de l'instrument de mesure vers la machine, se déroule de manière entièrement automatisée. Il est également possible de placer dans la cellule robotisée des systèmes de contrôle basés sur des caméras, un système de changement de préhenseur avec une aire de préhension pour le traitement d'un large éventail de pièces, de petites stations de lavage et de nettoyage, des systèmes d'ébavurage ou des stations de laser ou de gravure. Chaque station est alors également chargée et déchargée par le robot. Il en résulte donc un flux continu de pièces à travers différentes technologies. Pour un succès durable auprès de tous ses clients, EMAG mise sur des simulations informatisées lors de la planification des cellules d'automatisation. Les experts vérifient entre autres des facteurs tels que le temps de cycle, l'accessibilité, le flux de matériaux et le rendement pour les grandes lignes de production. La mise en service virtuelle - c'est-à-dire l'essai des processus et des interfaces sur le jumeau numérique de la ligne de production - est tout aussi importante. Cela permet de détecter des erreurs imprévues et de les éliminer dès les premières phases de développement. De plus, la mise en service "réelle" se déroule beaucoup plus rapidement par la suite.
"Dans l'ensemble, on peut certainement dire que de plus en plus de solutions robotisées sont utilisées sur nos machines, ce qui est toutefois évident", résume Jürgen Maier. "Après tout, nous disposons d'un grand nombre de machines qui disposent déjà d'une automatisation interne basée sur la technologie du pick-up. Par conséquent, nous pouvons intégrer assez facilement ces solutions robotisées dans des systèmes de production complets et établir un flux de pièces continu à travers de nombreuses technologies. Les activités manuelles tout au long de la chaîne de création de valeur sont donc en constante diminution. C'est notre approche, qui convainc de plus en plus de clients".
Interlocuteurs
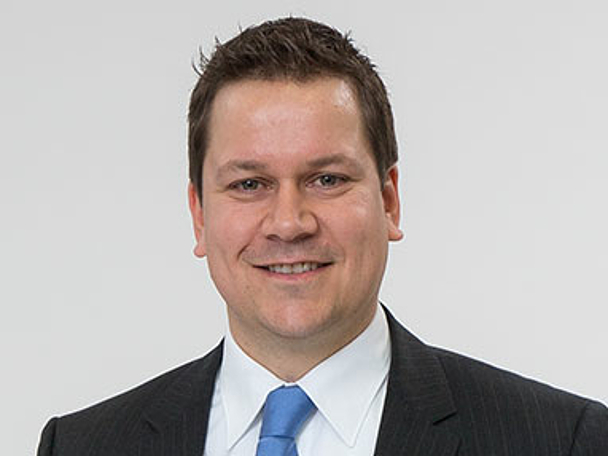
Oliver Hagenlocher
Zone
Press and Communication